28-01-2019
di Cesare Tava, Operation manager Bcube
di Cesare Tava, Operation manager Bcube
Quando mi sono trovato per la prima volta ad organizzare un inventario ho cercato supporto in letteratura, trovando vari testi da cui prendere spunti importanti, che trattano però la materia in modo parziale per singoli argomenti. Qui, pertanto, ho provato a trattare l’argomento in modo organico e completo, cercando di essere il più generale possibile per le varie tipologie e situazioni, dando così suggerimenti e spunti per affrontare questa attività che ciclicamente si ripete ogni anno.
Una piccola curiosità, il termine inventario può essere fuorviante, o come direbbero gli inglesi un “false friend”, non si vuole inventare nulla, ma il termine deriva dal verbo latino “invenire” che significa «trovare cercando, annotando le cose che si trovano in un dato luogo». L’inventario è un’attività che interessa tutti nodi della supply chain, dalle aree produttive (stazioni di montaggio, magazzini interoperazionali, ecc.) ai magazzini, centri distributivi, transit point, negozi, per allineare i quantitativi dei diversi item o codici tra fisico, cioè il reale quantitativo, e il contabile cioè quanto è registrato nei sistemi informativi o sui registri. L’inventario annuale o rotativo per l’azienda ha anche una valenza fiscale per la chiusura del bilancio e il conseguente inserimento e valorizzazione dei beni (a magazzino) nello stato patrimoniale, che dovrà in alcuni casi essere certificato da società terze che si occupano di revisione contabile, come nel caso di società quotate o per azioni.
I due valori fisico e contabile, per vari fattori, tra cui: errore umano, problemi informatici, ecc., con il tempo e le attività svolte sui materiali, tendono a disallinearsi. Un indicatore di quanto il magazzino “ruota”, che rappresenta l’intensità dell’attività, è l’indice di rotazione, cioè il rapporto tra:
Una piccola curiosità, il termine inventario può essere fuorviante, o come direbbero gli inglesi un “false friend”, non si vuole inventare nulla, ma il termine deriva dal verbo latino “invenire” che significa «trovare cercando, annotando le cose che si trovano in un dato luogo». L’inventario è un’attività che interessa tutti nodi della supply chain, dalle aree produttive (stazioni di montaggio, magazzini interoperazionali, ecc.) ai magazzini, centri distributivi, transit point, negozi, per allineare i quantitativi dei diversi item o codici tra fisico, cioè il reale quantitativo, e il contabile cioè quanto è registrato nei sistemi informativi o sui registri. L’inventario annuale o rotativo per l’azienda ha anche una valenza fiscale per la chiusura del bilancio e il conseguente inserimento e valorizzazione dei beni (a magazzino) nello stato patrimoniale, che dovrà in alcuni casi essere certificato da società terze che si occupano di revisione contabile, come nel caso di società quotate o per azioni.
I due valori fisico e contabile, per vari fattori, tra cui: errore umano, problemi informatici, ecc., con il tempo e le attività svolte sui materiali, tendono a disallinearsi. Un indicatore di quanto il magazzino “ruota”, che rappresenta l’intensità dell’attività, è l’indice di rotazione, cioè il rapporto tra:
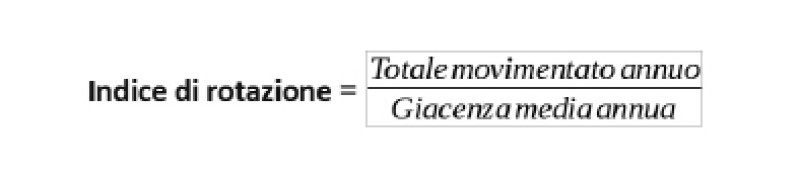
Tale rapporto espresso sia in quantità che in valore, dovrebbe dare nell’anno un risultato compreso tra 4-5 volte. Maggiore è il rapporto, maggiore è il materiale movimentato con tutti i possibili errori connessi. A questo punto la scelta da farsi è quella di decidere “Make or Buy”: se fare l’attività di inventario con le proprie risorse e mezzi (Make) o darla in gestione a società terze (Buy).
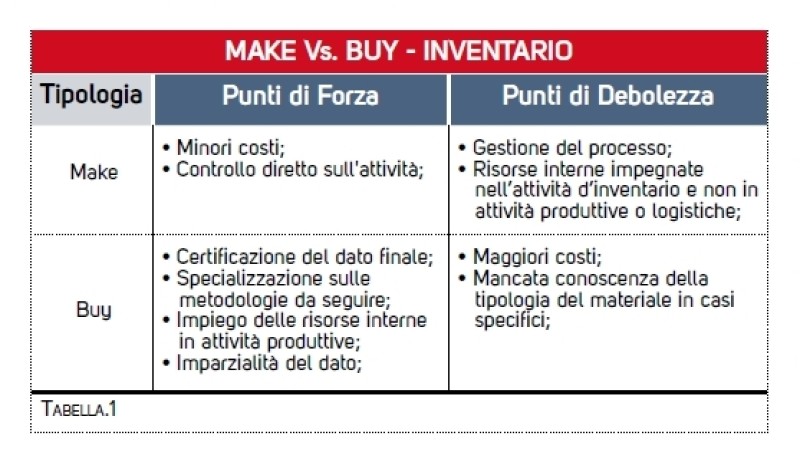
L’inventario può essere svolto con differenti modalità in base alle esigenze operative:
L’inventario completo può essere svolto a processo fermo o in attività e coinvolge in un breve periodo tutto il materiale a stock.
- Processo fermo, l’operatività giornaliera è ferma fino al completo conteggio dei pezzi o quantità per ogni codice, comprensivo di possibili seconde o terze conte.
- Processo in attività, ci troviamo in una situazione che i filosofi definirebbero di “Pántarêi”, cioè tutto scorre, la gestione dei dati risulta essere molto più complessa per tenere questi allineati fino al termine dell’inventario, prima di procedere con le rettifiche contabili.
Questa soluzione deve essere impiegata quando le attività non possono essere fermate o il tempo per un inventario completo non è sufficiente con il fermo delle attività produttive o di vendita. In questo ultimo caso si agirà in una situazione ibrida dove si inizierà a inventariare con il processo in attività, per poi trovarsi a processo fermo, e bisognerà valutare quali famiglie di materiali, per classe di rotazione – analisi di Pareto – o per aree, inventariare nei diversi momenti.
Inventario rotativo, il processo non viene fermato e con cadenza predefinita si procede a inventariare un numero definito di codici o aree per volta, durante tutto l’esercizio fiscale, registrarne i dati ed allineare i due magazzini, il fisico con il contabile. In entrambi i casi il materiale può essere inventariato una sola volta nell’esercizio, a meno di esigenze specifiche, per esempio per alto valore, materiale critico, ecc.
Inventario continuo, o "back-counting after picking", fatto direttamente dall’operatore che preleva. Tale attività implica un allungamento dei tempi di prelievo e quindi dei costi dell’attività, non può sostituire quello parziale o totale, ma permette un costate allineamento dei due magazzini e un maggior controllo del processo.
Analisi pre-inventario: andrà fatta una conta del numero di codici (divisi per categorie) e ubicazioni che saranno soggetti a inventario. Nel caso, i codici saranno divisi in famiglie per differente difficoltà o tipologie di conta (bulk, scaffali, magazzini esterni, conto-lavoristi, ecc.) e bisognerà individuare ed eliminare dalla conta tutti i codici obsoleti.
L’inventario completo può essere svolto a processo fermo o in attività e coinvolge in un breve periodo tutto il materiale a stock.
- Processo fermo, l’operatività giornaliera è ferma fino al completo conteggio dei pezzi o quantità per ogni codice, comprensivo di possibili seconde o terze conte.
- Processo in attività, ci troviamo in una situazione che i filosofi definirebbero di “Pántarêi”, cioè tutto scorre, la gestione dei dati risulta essere molto più complessa per tenere questi allineati fino al termine dell’inventario, prima di procedere con le rettifiche contabili.
Questa soluzione deve essere impiegata quando le attività non possono essere fermate o il tempo per un inventario completo non è sufficiente con il fermo delle attività produttive o di vendita. In questo ultimo caso si agirà in una situazione ibrida dove si inizierà a inventariare con il processo in attività, per poi trovarsi a processo fermo, e bisognerà valutare quali famiglie di materiali, per classe di rotazione – analisi di Pareto – o per aree, inventariare nei diversi momenti.
Inventario rotativo, il processo non viene fermato e con cadenza predefinita si procede a inventariare un numero definito di codici o aree per volta, durante tutto l’esercizio fiscale, registrarne i dati ed allineare i due magazzini, il fisico con il contabile. In entrambi i casi il materiale può essere inventariato una sola volta nell’esercizio, a meno di esigenze specifiche, per esempio per alto valore, materiale critico, ecc.
Inventario continuo, o "back-counting after picking", fatto direttamente dall’operatore che preleva. Tale attività implica un allungamento dei tempi di prelievo e quindi dei costi dell’attività, non può sostituire quello parziale o totale, ma permette un costate allineamento dei due magazzini e un maggior controllo del processo.
Analisi pre-inventario: andrà fatta una conta del numero di codici (divisi per categorie) e ubicazioni che saranno soggetti a inventario. Nel caso, i codici saranno divisi in famiglie per differente difficoltà o tipologie di conta (bulk, scaffali, magazzini esterni, conto-lavoristi, ecc.) e bisognerà individuare ed eliminare dalla conta tutti i codici obsoleti.
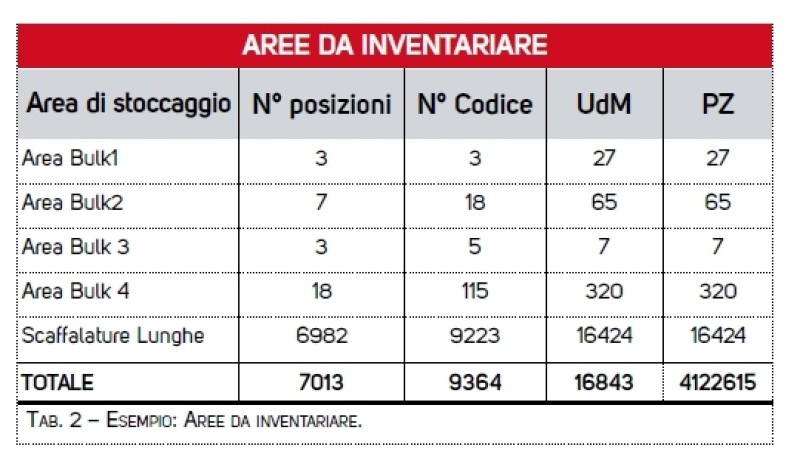
Tecnologia impiegata: Vi sono differenti possibilità per svolgere un inventario che andranno ad incidere sui tempi e risultati.
Questo dipenderà da:
- Tipo di materiale (dimensioni, caratteristiche fisiche).
- Specifiche di stoccaggio a bancale, cassa o collo mono-codice chiuso (che non prevede prelievi parziali), aperto o pluricodice, ecc.
- Valore del materiale.
Avremo le seguenti possibili soluzioni:
- Lista cartacea dei codici e posizioni da inventariare, identificazione della posizione del codice e conta manuale della quantità e registrazione di possibili seriali (S/N) o data di scadenza.
- Paperless tramite:
- Terminali pistola Radio Frequenza in cui l’attività di conta può essere lasciata all’operatore, ma l’identificazione del ma teriale (codice, seriale e scadenza) e della posizione e delle altre informazioni avviene tramite la lettura del barcode o QR Code;
- Voice picking in cui il terminale pistola è sostituito dal voice e dal ring scanner per la lettura del barcode. In entrambe le soluzioni tutta la merce e le locazioni dovranno presentare una etichetta con codice a barre.
Questo dipenderà da:
- Tipo di materiale (dimensioni, caratteristiche fisiche).
- Specifiche di stoccaggio a bancale, cassa o collo mono-codice chiuso (che non prevede prelievi parziali), aperto o pluricodice, ecc.
- Valore del materiale.
Avremo le seguenti possibili soluzioni:
- Lista cartacea dei codici e posizioni da inventariare, identificazione della posizione del codice e conta manuale della quantità e registrazione di possibili seriali (S/N) o data di scadenza.
- Paperless tramite:
- Terminali pistola Radio Frequenza in cui l’attività di conta può essere lasciata all’operatore, ma l’identificazione del ma teriale (codice, seriale e scadenza) e della posizione e delle altre informazioni avviene tramite la lettura del barcode o QR Code;
- Voice picking in cui il terminale pistola è sostituito dal voice e dal ring scanner per la lettura del barcode. In entrambe le soluzioni tutta la merce e le locazioni dovranno presentare una etichetta con codice a barre.
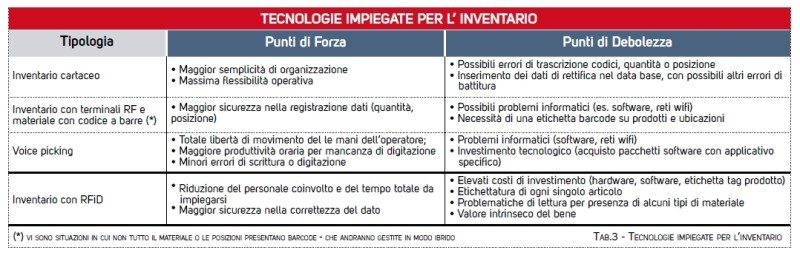
- Tecnologie RFiD in cui il conteggio e l’identificazione del materiale è lasciato alle tecnologia, tramite tag e antenne/ reader dove il tag (al cui interno sono registrate varie informazioni) può essere posto: sulla merce, packaging, pallet e sono presenti antenne fisse o mobili capaci di leggere i singoli tag e identificarne la posizione. Alcuni esempi:
- Punti vendita di abbigliamento di grandi catene dove tutti capi presentano tag RFid stampati all’interno del capo e antenne fisse posti all’interno degli scaffali dove viene esposta la merce, che permette il continuo monitoraggio della giacenza e innesca l’automatico riordino del materiale.
- Scansione di cataste di materiale poste in bulk, come elettrodomestici tramite antenne mobili poste su macchine robotizzate.
Questa tecnologia impone di valutare i costi e benefici, tangibili e intangibili tra costi del tag e attrezzature, valore del materiale e ritorno economico e di sicurezza.
Altri sistemi tecnologici:
- Tag GPS collocati sul materiale, per la geo-localizzazione.
- Droni che tramite fotocamere leggano le etichette sul materiale. Tali soluzioni vanno valutate in funzione del tipo di materiale, di stoccaggio e del loro valore.
Fase successiva, attribuire un tempo ciclo medio per inventariare uno specifico codice o ubicazione, per definire:
- Un monte ore per svolgere l’inventario.
- Il numero di risorse (Full Total Equivalent) per singola giornata o turni, in base al numero di conte previste.
In relazione a tutte le scelte sopra citate si propone un modello di valutazione che considera:
- I codici o posizioni da visitare.
- Il numero di squadre da creare in funzione dei mezzi (carrelli e terminali pistole RF) e risorse, ed il numero di risorse per squadra che ne varierà la produttività.
- Un range della produttività oraria a squadra realizzabile in base alla tecnologia scelta.
Al presente dimensionamento delle risorse dirette, andranno considerate anche le risorse indirette di ufficio per la gestione dei dati e delle anomalie.
- Punti vendita di abbigliamento di grandi catene dove tutti capi presentano tag RFid stampati all’interno del capo e antenne fisse posti all’interno degli scaffali dove viene esposta la merce, che permette il continuo monitoraggio della giacenza e innesca l’automatico riordino del materiale.
- Scansione di cataste di materiale poste in bulk, come elettrodomestici tramite antenne mobili poste su macchine robotizzate.
Questa tecnologia impone di valutare i costi e benefici, tangibili e intangibili tra costi del tag e attrezzature, valore del materiale e ritorno economico e di sicurezza.
Altri sistemi tecnologici:
- Tag GPS collocati sul materiale, per la geo-localizzazione.
- Droni che tramite fotocamere leggano le etichette sul materiale. Tali soluzioni vanno valutate in funzione del tipo di materiale, di stoccaggio e del loro valore.
Fase successiva, attribuire un tempo ciclo medio per inventariare uno specifico codice o ubicazione, per definire:
- Un monte ore per svolgere l’inventario.
- Il numero di risorse (Full Total Equivalent) per singola giornata o turni, in base al numero di conte previste.
In relazione a tutte le scelte sopra citate si propone un modello di valutazione che considera:
- I codici o posizioni da visitare.
- Il numero di squadre da creare in funzione dei mezzi (carrelli e terminali pistole RF) e risorse, ed il numero di risorse per squadra che ne varierà la produttività.
- Un range della produttività oraria a squadra realizzabile in base alla tecnologia scelta.
Al presente dimensionamento delle risorse dirette, andranno considerate anche le risorse indirette di ufficio per la gestione dei dati e delle anomalie.
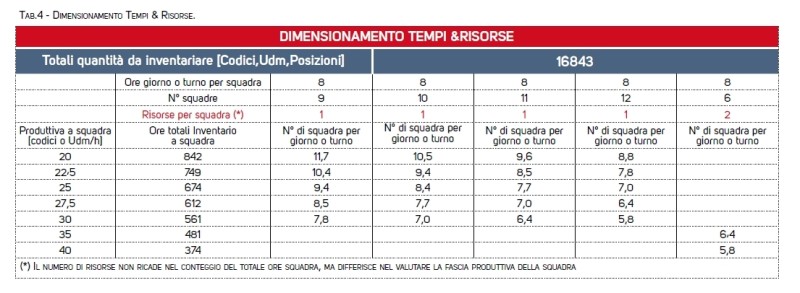
Definito il trade-off tra risorse disponibili e tempo massimo impiegabile per svolgere tale attività, si potrà così calendarizzare l’attività con un diagramma Gantt operativo:
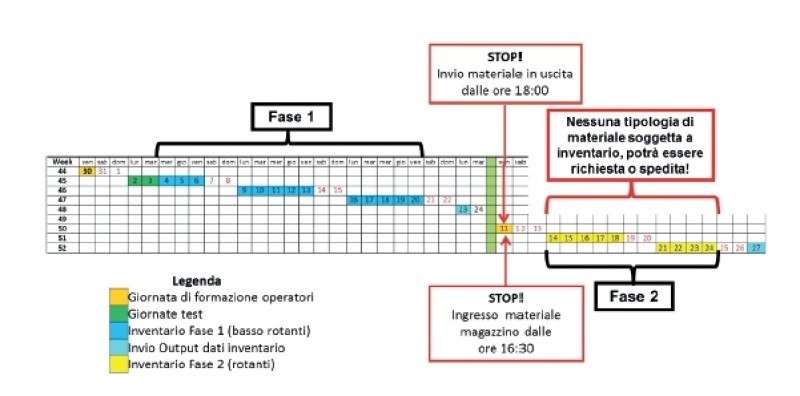
Il Gantt dovrà prevedere vari passi e alert, tra cui la formazione degli operatori su procedure e attrezzature, una fase di test per valutare la produttività, l’attività potrà essere divisa in due o più fasi in base alle tipologie di materiale (fase 1 non rotanti e fase 2 rotanti).
Standardizzazione delle procedure
Definire nei dettagli la procedura e descriverla con dei diagrammi di flusso e prevedere la gestione delle anomalie, come:
- Ubicazione piena e contabilmente vuota.
- Mancata identificazione del materiale per assenza dell’etichetta.
- E nel caso con terminale RF dare un worrying avendo inserito un quantitativo non coerente con quanto previsto a sistema e richiedere una seconda conta immediata.
Standardizzazione delle procedure
Definire nei dettagli la procedura e descriverla con dei diagrammi di flusso e prevedere la gestione delle anomalie, come:
- Ubicazione piena e contabilmente vuota.
- Mancata identificazione del materiale per assenza dell’etichetta.
- E nel caso con terminale RF dare un worrying avendo inserito un quantitativo non coerente con quanto previsto a sistema e richiedere una seconda conta immediata.
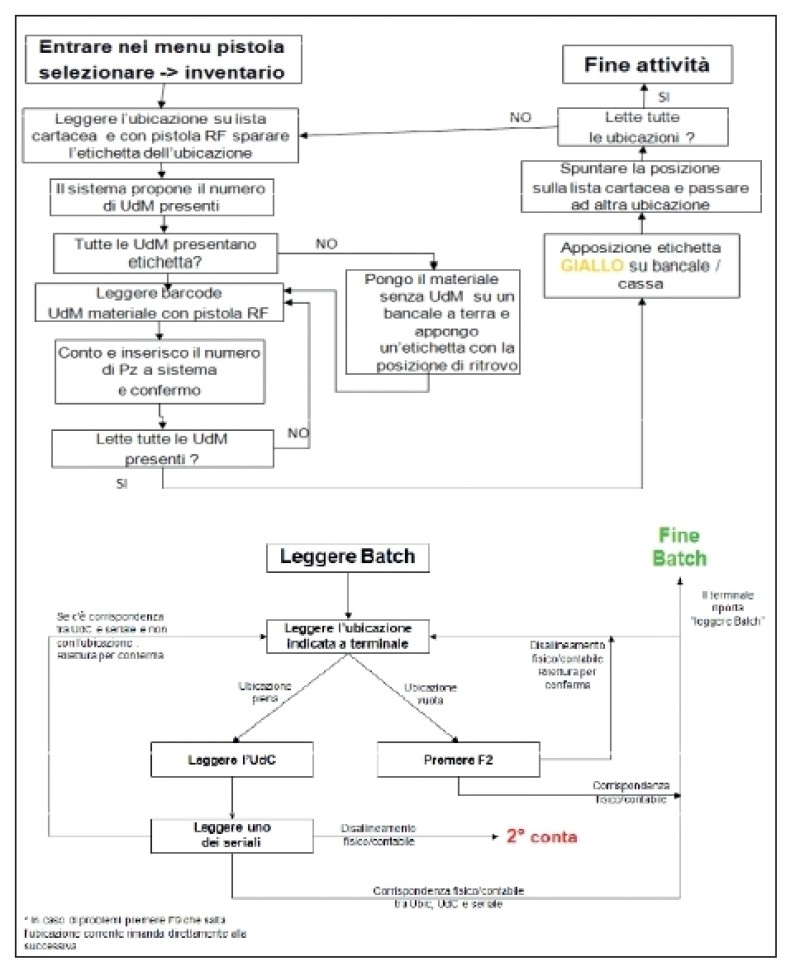
Piano formativo
Andrà previsto un piano formativo sulle procedure per le risorse, verificando la capacità degli operatori di utilizzare gli strumenti come: terminale pistola, WMS relativi alla gestione inventario, voice picking, bilance conta pezzi, piattaforme aree e di possedere il relativo patentino, ecc. In tale passaggio si verificherà la copertura wi-fi della zona e un test sul funzionamento del programma. Importante sarà identificare in modo ben visibile le posizioni inventariate, per una verifica visiva immediata dell’avanzamento e possibili dimenticanze, con una logica di visual management. Il segnalatore dovrà essere ben visibile anche ai livelli più alti (come si vede nella foto sotto, con i cartellini rossi), e in certi casi sfruttare questa occasione per identificare le merci in modo differente. Per esempio, i codici non rotanti, le aree di materiale rotante o il materiale presente in modalità di consignment stock, che non dovrà finire nei conteggi dell’inventario, perché materiale di proprietà del fornitore che diventerà del cliente solo nel momento del prelievo.
Andrà previsto un piano formativo sulle procedure per le risorse, verificando la capacità degli operatori di utilizzare gli strumenti come: terminale pistola, WMS relativi alla gestione inventario, voice picking, bilance conta pezzi, piattaforme aree e di possedere il relativo patentino, ecc. In tale passaggio si verificherà la copertura wi-fi della zona e un test sul funzionamento del programma. Importante sarà identificare in modo ben visibile le posizioni inventariate, per una verifica visiva immediata dell’avanzamento e possibili dimenticanze, con una logica di visual management. Il segnalatore dovrà essere ben visibile anche ai livelli più alti (come si vede nella foto sotto, con i cartellini rossi), e in certi casi sfruttare questa occasione per identificare le merci in modo differente. Per esempio, i codici non rotanti, le aree di materiale rotante o il materiale presente in modalità di consignment stock, che non dovrà finire nei conteggi dell’inventario, perché materiale di proprietà del fornitore che diventerà del cliente solo nel momento del prelievo.
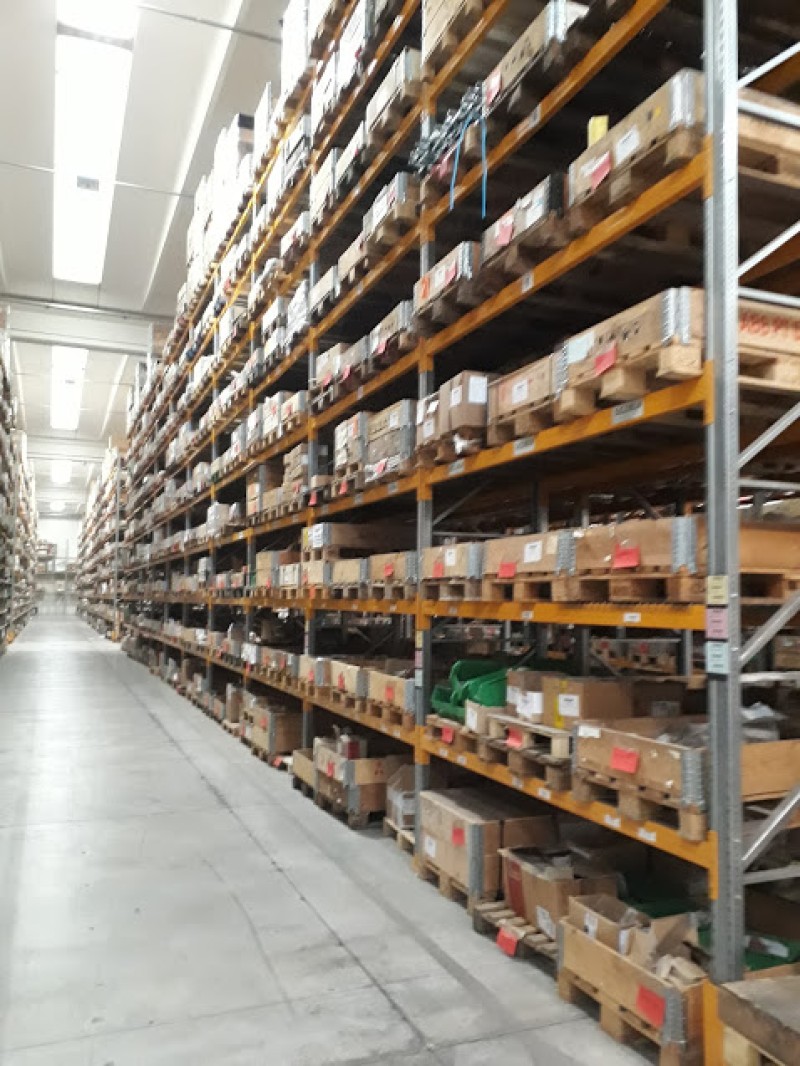
Avanzamento inventario
L’inventario deve durare un tempo definito a priori, per non inficiare le attività produttive o logistiche, quindi sarà monitorato l’avanzamento dello stesso nel tempo e confrontato con il forecast previsto. Per il monitoraggio dell’avanzamento dell’inventario si costruirà un grafico che chiameremo Piano Avanzamento Inventario, che richiederà un aggiornamento costante:
L’inventario deve durare un tempo definito a priori, per non inficiare le attività produttive o logistiche, quindi sarà monitorato l’avanzamento dello stesso nel tempo e confrontato con il forecast previsto. Per il monitoraggio dell’avanzamento dell’inventario si costruirà un grafico che chiameremo Piano Avanzamento Inventario, che richiederà un aggiornamento costante:
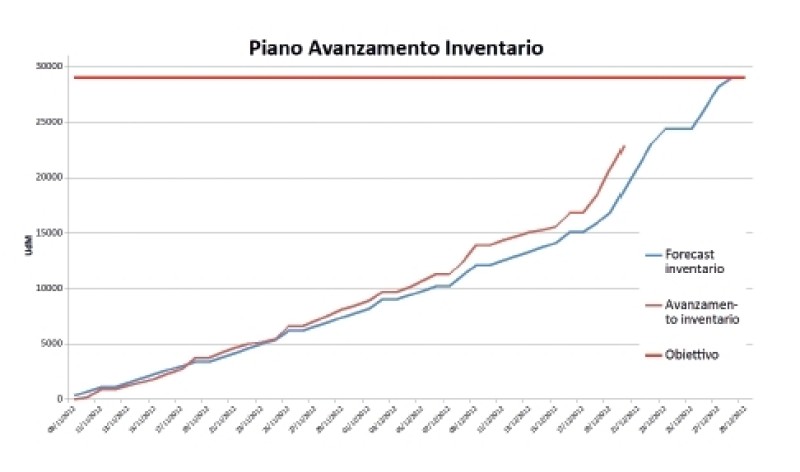
L’inventario in numeri. Al termine dell’inventario andranno incrociati i dati fisici e contabili in termini di quantità, valore e posizione. Prima di sovrascrivere i primi sui secondi, si dovrà verificare:
- Se il materiale si trova nella stessa ubicazione riscontrata all’inventario.
- Il delta delle quantità tra fisico e contabile, ordinate in modo decrescente fino a un valore minimo definito. Tali delta possono essere anche attribuibili ad errori di digitazione o scrittura (raddoppio di cifre) spesso correggibili senza una verifica fisica.
- I delta in termini di valore ordinati in modo decrescente, fino a un valore minimo definito.
- I delta di quantità per materiali critici o strategici.
Questi elenchi così creati, depurati dei possibili doppioni o nel caso di codici di classe zero rotante, potranno dar vita alla seconda o terza conta, e con operatori diversi dalla prima. Svolte tutte le verifiche si procederà a sovrascrivere le giacenze contabili con il dato dell’inventario e analizzare il risultato in termini di: quantità, codici e valore con grafici a istogrammi a fasce non omogenee (come in Figura 4), ma crescenti degli errori riscontrati, che produrrà una distribuzione a campana. Emerge subito, nell’esempio in figura, che l’errore principale che si è verificato, è l’errata conta di pezzi nella fascia dei cinque pezzi, per via della tipologia del materiale, mediamente piccolo e prelevato in quantità sfuse, che presenta una distribuzione delle code simmetrica, segno di un errore fisiologico. Tali analisi si posso fare per famiglia di prodotto o customizzare in relazione alla tipologia del materiale gestito.
- Se il materiale si trova nella stessa ubicazione riscontrata all’inventario.
- Il delta delle quantità tra fisico e contabile, ordinate in modo decrescente fino a un valore minimo definito. Tali delta possono essere anche attribuibili ad errori di digitazione o scrittura (raddoppio di cifre) spesso correggibili senza una verifica fisica.
- I delta in termini di valore ordinati in modo decrescente, fino a un valore minimo definito.
- I delta di quantità per materiali critici o strategici.
Questi elenchi così creati, depurati dei possibili doppioni o nel caso di codici di classe zero rotante, potranno dar vita alla seconda o terza conta, e con operatori diversi dalla prima. Svolte tutte le verifiche si procederà a sovrascrivere le giacenze contabili con il dato dell’inventario e analizzare il risultato in termini di: quantità, codici e valore con grafici a istogrammi a fasce non omogenee (come in Figura 4), ma crescenti degli errori riscontrati, che produrrà una distribuzione a campana. Emerge subito, nell’esempio in figura, che l’errore principale che si è verificato, è l’errata conta di pezzi nella fascia dei cinque pezzi, per via della tipologia del materiale, mediamente piccolo e prelevato in quantità sfuse, che presenta una distribuzione delle code simmetrica, segno di un errore fisiologico. Tali analisi si posso fare per famiglia di prodotto o customizzare in relazione alla tipologia del materiale gestito.
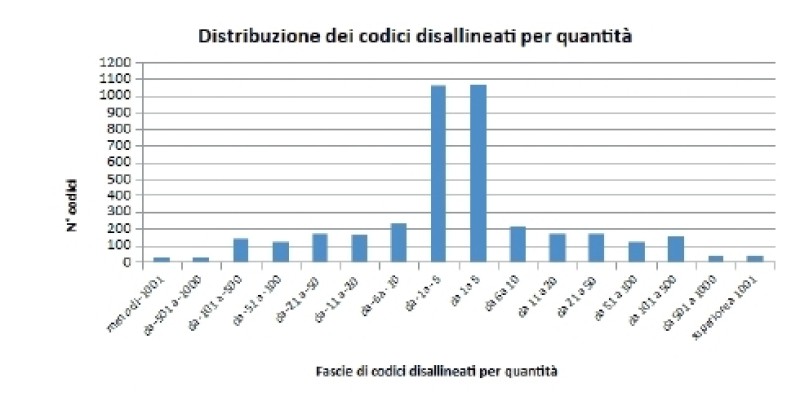
Un corretto inventario e quindi una corretta giacenza, permette di avere un’affidabilità delle scorte e tutela da possibili rotture di stock, che impongono in altro caso, nel calcolo della gestione delle scorte, di tenere presente non solo la variabilità della domanda, ma anche l’accuratezza della giacenza, soprattutto per i materiali critici, o con un alto lead time di approvvigionamento. L’indice di accuratezza dell’inventario in termini gestionale/ operativo è dato dal rapporto tra:
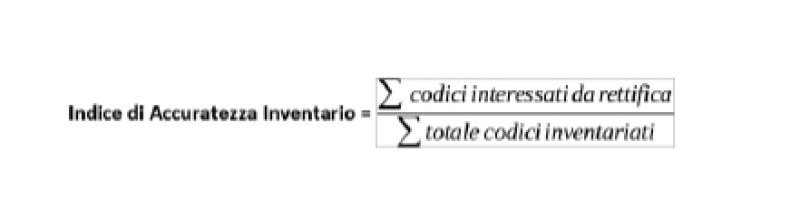
L’indice dà un’immediata percezione dello stato del magazzino e dovrà oscillare tra 95–100%, in base al tipo di materiale e al processo.
Una variante di questo è quella che si basa sull’indice di rotazione per codice, così se un codice è di classe C ed ha presentato un delta inventariale entro un limite di tolleranza % assegnato, tale codice non sarà considerato tra quelli rettificati.
I limiti di tolleranza per classe di rotazione sono tipicamente:
- Classe A: 0%
- Classe B: ±2% massimo.
- Classe C: ±5% massimo.
In caso di gestione dei materiali con logica FIFO o LIFO, in cui il materiale in ingresso dello stesso codice, anche se compattabile con quello già stoccato, non può essere allocato nella medesima posizione (per differenti lotti di produzione, di scadenza, o data di ingresso in magazzino), introdurrà un sotto insieme del codice che chiameremo “Unità di Movimentazione” e gestiremo questi, come codici a sé stanti.
Dal punto di vista amministrativo/ contabile, gli indici considereranno il valore del materiale inventariato e potremo averne due:
- Valore assoluto.
- Valore algebrico.
Il primo rappresenta l’accuratezza dell’inventario, mentre il secondo evidenzia le perdite o guadagni che andranno a essere inserite nel bilancio aziendale.
Il valore del materiale attribuito a ogni singolo codice è dato dal costo di acquisto pieno o scontato o di produzione, calcolato sulla media degli acquisti o della produzione nell’anno. Tale valore è anche chiamato Prezzo Medio Ponderato (PMP) o Costo Medio Ponderato (CMP).
L’inventario nel contratto di servizio
Se le attività di stoccaggio e movimentazione sono lasciate a società terze tipicamente provider logistici, la voce inventario e la sua regolamentazione deve essere sempre inserita nel contratto.
Il fornitore, al momento di sottoscrivere il contratto, dovrà definire se tutta la gestione informatica sarà tenuta sui sistemi informativi del cliente (ad esempio SAP) o sul suo WMS.
Qui andranno definiti tempi e modi di copia dei dati del magazzino, se già esistente, e quindi tempi (durante un periodo senza attività di produzione, ricezione o spedizione) e costi dell’inventario zero; da quel momento il provider prenderà la responsabilità della giacenza.
Nel caso di un nuovo magazzino sarà la registrazione degli ingressi a creare la giacenza. In entrambi i casi si definirà anche l’interfaccia di scambio giornaliero dei dati.
Tipicamente tali clausole presentano un fattore compensativo tra rettifiche inventariali positive e negative e un valore di franchigia per il fornitore. Troveremo per tanto nel contratto le seguenti formulazioni:
- Al termine dell’inventario, le eventuali differenze (negativo o positivo) tra quantità contabili e quantità fisiche del magazzino saranno verificate in contraddittorio tra le parti, e valorizzate per ciascun codice al PMP dando origine al Valore delle Rettifiche inventariali Negative (VRN) e Valorizzazioni delle Rettifiche Inventariali Positive (VRP) sommate algebricamente.
Le differenze risultanti, se negative, daranno luogo all’obbligo per il fornitore di corrispondere al cliente un importo pari al valore del saldo negativo, al netto del valore della franchigia.
- Il valore della franchigia varierà in base al contesto e al tipo di materiale inventariato, ed è calcolato in percentuale sul valore del materiale inventariato; tale percentuale potrebbe essere compresa tra 0,007 e 0,003 tipicamente si definisce un inventario zero e in funzione del delta algebrico o del valore assoluto e in base alle aspettative ed esigenze si definisce quello che potrebbe essere un valore accettabile e da quello partire per definire un piano decrementale negli anni del valore di franchigia da inserire nel contratto, per esempio:
• 1° anno: da definire;
• 2° anno: 0,5%;
• 3° anno: 0,3%.
Gli indicatori di riferimento KPI saranno:
Una variante di questo è quella che si basa sull’indice di rotazione per codice, così se un codice è di classe C ed ha presentato un delta inventariale entro un limite di tolleranza % assegnato, tale codice non sarà considerato tra quelli rettificati.
I limiti di tolleranza per classe di rotazione sono tipicamente:
- Classe A: 0%
- Classe B: ±2% massimo.
- Classe C: ±5% massimo.
In caso di gestione dei materiali con logica FIFO o LIFO, in cui il materiale in ingresso dello stesso codice, anche se compattabile con quello già stoccato, non può essere allocato nella medesima posizione (per differenti lotti di produzione, di scadenza, o data di ingresso in magazzino), introdurrà un sotto insieme del codice che chiameremo “Unità di Movimentazione” e gestiremo questi, come codici a sé stanti.
Dal punto di vista amministrativo/ contabile, gli indici considereranno il valore del materiale inventariato e potremo averne due:
- Valore assoluto.
- Valore algebrico.
Il primo rappresenta l’accuratezza dell’inventario, mentre il secondo evidenzia le perdite o guadagni che andranno a essere inserite nel bilancio aziendale.
Il valore del materiale attribuito a ogni singolo codice è dato dal costo di acquisto pieno o scontato o di produzione, calcolato sulla media degli acquisti o della produzione nell’anno. Tale valore è anche chiamato Prezzo Medio Ponderato (PMP) o Costo Medio Ponderato (CMP).
L’inventario nel contratto di servizio
Se le attività di stoccaggio e movimentazione sono lasciate a società terze tipicamente provider logistici, la voce inventario e la sua regolamentazione deve essere sempre inserita nel contratto.
Il fornitore, al momento di sottoscrivere il contratto, dovrà definire se tutta la gestione informatica sarà tenuta sui sistemi informativi del cliente (ad esempio SAP) o sul suo WMS.
Qui andranno definiti tempi e modi di copia dei dati del magazzino, se già esistente, e quindi tempi (durante un periodo senza attività di produzione, ricezione o spedizione) e costi dell’inventario zero; da quel momento il provider prenderà la responsabilità della giacenza.
Nel caso di un nuovo magazzino sarà la registrazione degli ingressi a creare la giacenza. In entrambi i casi si definirà anche l’interfaccia di scambio giornaliero dei dati.
Tipicamente tali clausole presentano un fattore compensativo tra rettifiche inventariali positive e negative e un valore di franchigia per il fornitore. Troveremo per tanto nel contratto le seguenti formulazioni:
- Al termine dell’inventario, le eventuali differenze (negativo o positivo) tra quantità contabili e quantità fisiche del magazzino saranno verificate in contraddittorio tra le parti, e valorizzate per ciascun codice al PMP dando origine al Valore delle Rettifiche inventariali Negative (VRN) e Valorizzazioni delle Rettifiche Inventariali Positive (VRP) sommate algebricamente.
Le differenze risultanti, se negative, daranno luogo all’obbligo per il fornitore di corrispondere al cliente un importo pari al valore del saldo negativo, al netto del valore della franchigia.
- Il valore della franchigia varierà in base al contesto e al tipo di materiale inventariato, ed è calcolato in percentuale sul valore del materiale inventariato; tale percentuale potrebbe essere compresa tra 0,007 e 0,003 tipicamente si definisce un inventario zero e in funzione del delta algebrico o del valore assoluto e in base alle aspettative ed esigenze si definisce quello che potrebbe essere un valore accettabile e da quello partire per definire un piano decrementale negli anni del valore di franchigia da inserire nel contratto, per esempio:
• 1° anno: da definire;
• 2° anno: 0,5%;
• 3° anno: 0,3%.
Gli indicatori di riferimento KPI saranno:
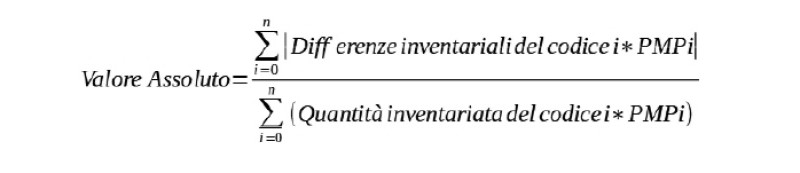
L’indicatore dovrà risultare minore o uguale al 1% (in base alla realtà).
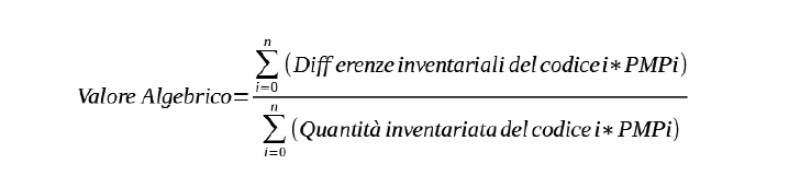
L’indicatore dovrà risultare minore o uguale al 0,5% (in base alla realtà).
Il valore Target sarà 99% con il valore minimo a 95% se si scende al di sotto nell’inventario completo, o in quello rotativo, per un prolungato periodo di tempo (ad esempio: tre mesi), quindi in presenza di un processo fuori controllo, la necessità di svolgere inventari rotativi ravvicinati o uno intero Wall to Wall da parte del fornitore fino a raggiungere il livello target KPI, e definire degli action plan come “back-counting after picking” per ridurre gli errori durate l’attività.
Costo operativo dell’inventario
Tali costi possono essere annegati nelle varie voci dell’impianto tariffario, tipicamente nel caso di inventario completo o essere creata una tariffa ad hoc per unità (codice, collo, ecc.) inventariata nel caso di inventario rotativo. Il costo totale è la sommatoria delle ore delle risorse, dei mezzi (affitto di carrelli, piattaforme aeree), degli strumenti impiegati (affitto di conta pezzi o pistole RF aggiuntive).
L'inventario 4.0
L’inventario era già stato interessato da ridimensionamento con la riduzione delle giacenze grazie:
- all’introduzione della lean e del concetto del zero scorte con l’uso del kanban, e logiche di gestione (pull);
- alla riduzione, sempre più restringente dei lead time di approvvigionamento, lungo tutta la supply chain, con logiche di gestione tradizionali (push), e quindi del tempo di riordino con la conseguente riduzione del lotto economico (EOQ) e delle scorte di sicurezza.
Oggi siamo alle porte di nuovo cambiamento, che rivoluziona tutta l’azienda, con il paradigma industria 4.0 che ha l’obiettivo di creare “flussi produttivi integrati (cliente fornitore), automatizzati e globalmente ottimizzati ad alta flessibilità”. Anche l’attività di inventario subirà la pervasività di tale rivoluzione, andando a creare un concetto di inventario 4.0.
Questa nuova metodologia di fare industria si basa su nove pilastri di tecnologie mature (Figura 5), e l’inventario ne sfrutta alcuni (quelli in rosso):
Il valore Target sarà 99% con il valore minimo a 95% se si scende al di sotto nell’inventario completo, o in quello rotativo, per un prolungato periodo di tempo (ad esempio: tre mesi), quindi in presenza di un processo fuori controllo, la necessità di svolgere inventari rotativi ravvicinati o uno intero Wall to Wall da parte del fornitore fino a raggiungere il livello target KPI, e definire degli action plan come “back-counting after picking” per ridurre gli errori durate l’attività.
Costo operativo dell’inventario
Tali costi possono essere annegati nelle varie voci dell’impianto tariffario, tipicamente nel caso di inventario completo o essere creata una tariffa ad hoc per unità (codice, collo, ecc.) inventariata nel caso di inventario rotativo. Il costo totale è la sommatoria delle ore delle risorse, dei mezzi (affitto di carrelli, piattaforme aeree), degli strumenti impiegati (affitto di conta pezzi o pistole RF aggiuntive).
L'inventario 4.0
L’inventario era già stato interessato da ridimensionamento con la riduzione delle giacenze grazie:
- all’introduzione della lean e del concetto del zero scorte con l’uso del kanban, e logiche di gestione (pull);
- alla riduzione, sempre più restringente dei lead time di approvvigionamento, lungo tutta la supply chain, con logiche di gestione tradizionali (push), e quindi del tempo di riordino con la conseguente riduzione del lotto economico (EOQ) e delle scorte di sicurezza.
Oggi siamo alle porte di nuovo cambiamento, che rivoluziona tutta l’azienda, con il paradigma industria 4.0 che ha l’obiettivo di creare “flussi produttivi integrati (cliente fornitore), automatizzati e globalmente ottimizzati ad alta flessibilità”. Anche l’attività di inventario subirà la pervasività di tale rivoluzione, andando a creare un concetto di inventario 4.0.
Questa nuova metodologia di fare industria si basa su nove pilastri di tecnologie mature (Figura 5), e l’inventario ne sfrutta alcuni (quelli in rosso):
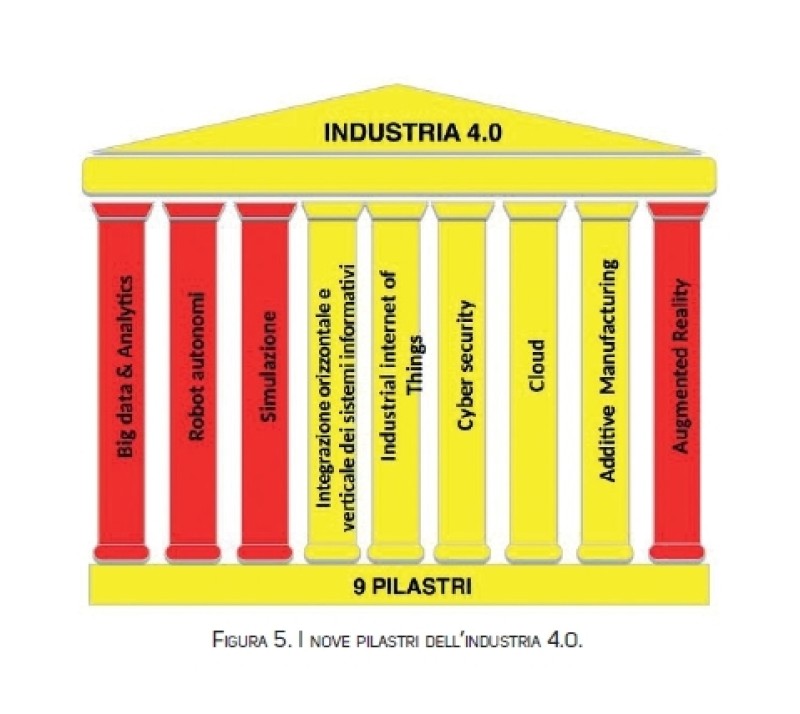
- Big data & Analytics: raccolta di dati provenienti da differenti fonti a supporto del processo decisionale, tra cui il dato della giacenze di tutta la supply chain in tempo reale, grazie a materiali che interagiscono con i vari device dichiarandone la presenza e la quantità.
- Robot autonomi: robot a basso costo e che hanno la capacità di integrarsi tra di loro e con le attività dell’uomo; attività di inventario svolte da droni e robot, che permettono di svolgere più inventari nell’anno, sempre interconnesso con i dati contabili, aggiornandoli e riducendo la richiesta di forza lavoro.
- Simulazione: elaborando dati in tempo reale e poi valutando azioni da intraprendere nel breve, questo grazie anche a dati sempre aggiornati in tempo reale delle giacenze e potendo valutare il mix da produrre/ vendere in base alle reali possibilità.
- Augmented Reality: sono sistemi multimediali come smartphone, occhiali (ad esempio: Google Glass), auricolari e manipolatori (guanti) che aggiungono informazioni multimediali alla realtà operativa; nel caso dell’inventario l’introduzione di occhiali che permettono il riconoscimento dei prodotti tramite visori ottici integrati con altri sistemi per il riconoscimento del materiale e la loro conta e definizione della posizione. Questo nuovo passo sarà incentrato a un idea di aumentare la connettività tra materiali e macchine, sfruttando appieno le tecnologie a vari livelli e riducendo la forza lavoro impiegata.
- Robot autonomi: robot a basso costo e che hanno la capacità di integrarsi tra di loro e con le attività dell’uomo; attività di inventario svolte da droni e robot, che permettono di svolgere più inventari nell’anno, sempre interconnesso con i dati contabili, aggiornandoli e riducendo la richiesta di forza lavoro.
- Simulazione: elaborando dati in tempo reale e poi valutando azioni da intraprendere nel breve, questo grazie anche a dati sempre aggiornati in tempo reale delle giacenze e potendo valutare il mix da produrre/ vendere in base alle reali possibilità.
- Augmented Reality: sono sistemi multimediali come smartphone, occhiali (ad esempio: Google Glass), auricolari e manipolatori (guanti) che aggiungono informazioni multimediali alla realtà operativa; nel caso dell’inventario l’introduzione di occhiali che permettono il riconoscimento dei prodotti tramite visori ottici integrati con altri sistemi per il riconoscimento del materiale e la loro conta e definizione della posizione. Questo nuovo passo sarà incentrato a un idea di aumentare la connettività tra materiali e macchine, sfruttando appieno le tecnologie a vari livelli e riducendo la forza lavoro impiegata.