06-02-2020
Con il suo consueto evento europeo tenutosi a fine gennaio, "Innovations & Highlights 2020", Jungheinrich ha lanciato sul mercato una rosa molto ampia di novità, accompagnate da idee e progetti che segnano il ruolo dell’azienda sul mercato.
Il mercato mondiale dei carrelli, illustra Christian Erlach, membro del consiglio amministrazione con responsabilità alle vendite di Jungheinrich, ha raggiunto nel 2019 il numero di 1.507 mila unità (fonte WITS, World Industrial Truck Statistics). Di questi, il 47% sono macchine da magazzino, il 17% sono controbilanciati elettrici e solo il 36% sono controbilanciati termici. Il mercato europeo ed est Europeo assorbono rispettivamente il 27 e il 6% delle vendite.
I risultati per Jungheinrich, al netto dell’ultimo trimestre (l’anno fiscale per Jungheinrich si conclude a marzo), hanno sostanzialmente superato le previsioni di inizio anno, anche se secondo l’azienda si percepiscono segnali di assestamento soprattutto per l’anno appena cominciato. Pur delineando questo scenario di grande attenzione, Jungheinrich sta portando avanti un ragguardevole programma di investimenti e di innovazioni. Ad esempio con una nuova sede inaugurata a settembre 2019 (dove lavoreranno oltre mille persone e premiata dal German Sustainable Building Council per le elevate caratteristiche di sostenibilità ambientale) e con l’ingresso di nuovi manager nella squadra, con particolare riferimento a Sabine Neuß che entra nel consiglio di amministrazione come responsabile Engineering. Ma anche e soprattutto con le novità sul fronte delle nuove batterie e relativi sistemi di ricarica e stoccaggio energia, che entreranno sul mercato nei prossimi mesi. Il fronte delle batterie agli ioni di litio, infatti, è di grandissimo interesse. Rispetto ai 1641 pezzi venduti nel 2016, oggi Jungheinrich è passata a circa 15mila carrelli venduti nel 2019 dotati di nuove batterie - e per il 2025 si prevede che l'80% dei carrelli Jungheinrich avranno batterie agli ioni di litio. Questo l’obiettivo attuale di Jungheinrich: diventare il leader europeo nello sviluppo, produzione, riciclo e utilizzo ecologico di sistemi di energia per i carrelli elevatori e i sistemi di movimentazione interna.
Il mercato mondiale dei carrelli, illustra Christian Erlach, membro del consiglio amministrazione con responsabilità alle vendite di Jungheinrich, ha raggiunto nel 2019 il numero di 1.507 mila unità (fonte WITS, World Industrial Truck Statistics). Di questi, il 47% sono macchine da magazzino, il 17% sono controbilanciati elettrici e solo il 36% sono controbilanciati termici. Il mercato europeo ed est Europeo assorbono rispettivamente il 27 e il 6% delle vendite.
I risultati per Jungheinrich, al netto dell’ultimo trimestre (l’anno fiscale per Jungheinrich si conclude a marzo), hanno sostanzialmente superato le previsioni di inizio anno, anche se secondo l’azienda si percepiscono segnali di assestamento soprattutto per l’anno appena cominciato. Pur delineando questo scenario di grande attenzione, Jungheinrich sta portando avanti un ragguardevole programma di investimenti e di innovazioni. Ad esempio con una nuova sede inaugurata a settembre 2019 (dove lavoreranno oltre mille persone e premiata dal German Sustainable Building Council per le elevate caratteristiche di sostenibilità ambientale) e con l’ingresso di nuovi manager nella squadra, con particolare riferimento a Sabine Neuß che entra nel consiglio di amministrazione come responsabile Engineering. Ma anche e soprattutto con le novità sul fronte delle nuove batterie e relativi sistemi di ricarica e stoccaggio energia, che entreranno sul mercato nei prossimi mesi. Il fronte delle batterie agli ioni di litio, infatti, è di grandissimo interesse. Rispetto ai 1641 pezzi venduti nel 2016, oggi Jungheinrich è passata a circa 15mila carrelli venduti nel 2019 dotati di nuove batterie - e per il 2025 si prevede che l'80% dei carrelli Jungheinrich avranno batterie agli ioni di litio. Questo l’obiettivo attuale di Jungheinrich: diventare il leader europeo nello sviluppo, produzione, riciclo e utilizzo ecologico di sistemi di energia per i carrelli elevatori e i sistemi di movimentazione interna.
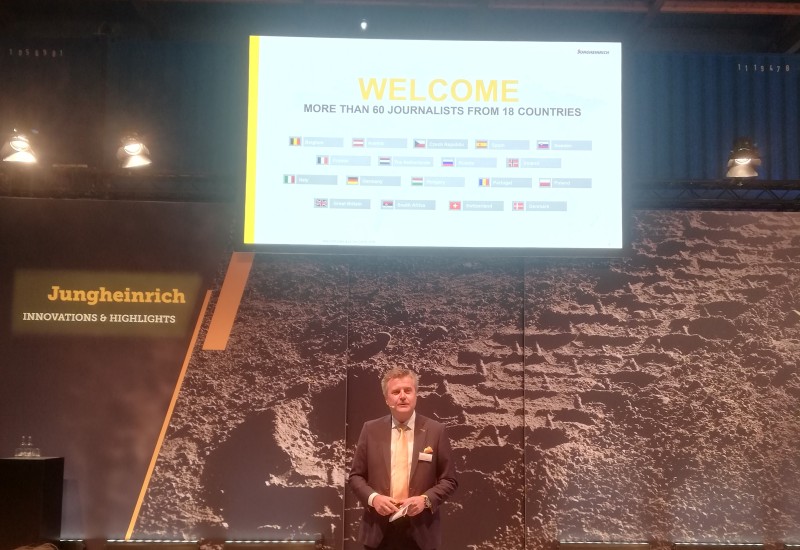
Ancora novità sulla combustione interna
Oggi, il 98% dei carrelli venduti da Jungheinrich sono elettrici. Tuttavia, come spiegato da Marek Scheithauer e Sebastian Voit, esiste ancora una consistente fascia di mercato che richiede carrelli a combustione interna. E, visto che Jungheinrich intende rimanere ai vertici in tutti i settori della movimentazione interna, ha lanciato in questi giorni una nuova generazione di idrostatici, in versione gas e diesel, in collaborazione con Kubota per la fornitura dei motori.
Le caratteristiche dei nuovi modelli sono di alto livello: seduta super ergonomica, riscaldamento in cabina, ma anche prestazioni ai vertici, stabilità, equilibrio, consumi ridotti al minimo e motori dotati di filtro antiparticolato. Dato che, come noto, il motore IC richiede più manutenzione dell’elettrico, l’accesso al motore è stato opportunamente agevolato.
Le due serie di veicoli idrostatici controbilanciati si chiamano VFG 3s e 4s, e sono disponibili anche per le applicazioni indoor (dove consentite). Comprendono otto varianti e coprono carichi da 1,6 t a to 3,5 t. Per quanto riguarda i gas di scarico, i nuovi carrelli rispettano i criteri europei di stage V. Dal punto di vista meccanico sono dotati di tecnologia idrostatica, che consente un’efficace movimentazione contenendo i consumi di energia. Dal punto di vista dell’ergonomia, il tetto panoramico è stato ampliato del 25%, e ulteriormente abbassato il cruscotto per aumentare la visibilità generale. I nuovi VFG sono dotati di tecnologia telematica, con la quale l’utente può controllare tutta l’operatività dei carrelli.
Le principali novità sul fronte delle batterie agli ioni di litio
La principale novità che vede la luce in questa occasione è il controbilanciato EFG P30i, “nativamente” agli ioni di litio, con batterie ad alta potenza: 96 V. Questa nuova soluzione, presentata in anteprima ma non disponibile sul mercato prima della fine del 2021, sarà il ponte naturale fra diesel ed elettrico: le sue prestazioni saranno assolutamente analoghe a quelle dei veicoli a motore. Il tutto grazie ad una progettazione completamente rinnovata. Le batterie agli ioni di litio sono posizionate in due vani separati: in questo modo lo spazio per le gambe è raddoppiato e anche la visibilità è decisamente aumentata. Le batterie sono riscaldate, in modo da non perdere in prestazioni durante i mesi invernali.
Il veicolo è progettato per utilizzi gravosi e prevalentemente per esterni; anche gli pneumatici sono scelti per l’uso in esterno. Il veicolo è dotato di due motori elettrici, alimentati da due moduli batteria da 25 kWh ciascuno, che consentono al carrello di coprire fino a tre turni di lavoro. Anche la presa di ricarica è ridisegnata e ottimizzata per semplificare le attività di ricarica, che può avvenire anche all’esterno.
Il nuovo concetto prende il meglio dei due mondi: la sua velocità di sollevamento supera del 25% quella dei classici carrelli controbilanciati elettrici; anche la capacità di andare in salita è aumentata di un terzo rispetto alla media degli elettrici. Le batterie agli ioni di litio inoltre hanno consentito ai progettisti di gestire il peso in modo completamente diverso rispetto ai normali carrelli elettrici, condizionati dalla forma della batteria. Questo aumenta l’agilità del carrello, riducendo nel contempo il consumo di energia.
Oltre allo spazio interno che è letteralmente raddoppiato, grazie alla forma delle batterie, anche la visibilità esterna è stata migliorata: con effetti positivi sulla sicurezza del lavoro. Un passo importante, dunque, sulla via di una logistica ad emissioni zero, sulla quale Jungheinrich è fermamente impegnata. Se calcoliamo tutta la sua vita utile, il nuovo carrello consentirà di risparmiare circa il 52% di CO2 rispetto a un normale carrello a combustione interna, considerando l’attuale mix energetico europeo e tenendo conto della maggior energia richiesta per la sua produzione.
Le batterie agli ioni di litio scelte da Jungheinrich, infine, sono in particolare del tipo litio-ferro-fosfato, dunque non richiedono la presenza di cobalto e non confliggono con altre industrie che fanno uso di batterie di nuova generazione, riducendo i rischi connessi agli approvvigionamenti.
Questo dunque il futuro: non dovremo usare più i carrelli a combustione interna. Dunque – chiedono dal pubblico – i carrelli VFG presentati in precedenza, potrebbero essere gli ultimi che Jungheinrich propone con questo tipo di motori? «Sì» è la risposta di Christian Erlach.
Oggi, il 98% dei carrelli venduti da Jungheinrich sono elettrici. Tuttavia, come spiegato da Marek Scheithauer e Sebastian Voit, esiste ancora una consistente fascia di mercato che richiede carrelli a combustione interna. E, visto che Jungheinrich intende rimanere ai vertici in tutti i settori della movimentazione interna, ha lanciato in questi giorni una nuova generazione di idrostatici, in versione gas e diesel, in collaborazione con Kubota per la fornitura dei motori.
Le caratteristiche dei nuovi modelli sono di alto livello: seduta super ergonomica, riscaldamento in cabina, ma anche prestazioni ai vertici, stabilità, equilibrio, consumi ridotti al minimo e motori dotati di filtro antiparticolato. Dato che, come noto, il motore IC richiede più manutenzione dell’elettrico, l’accesso al motore è stato opportunamente agevolato.
Le due serie di veicoli idrostatici controbilanciati si chiamano VFG 3s e 4s, e sono disponibili anche per le applicazioni indoor (dove consentite). Comprendono otto varianti e coprono carichi da 1,6 t a to 3,5 t. Per quanto riguarda i gas di scarico, i nuovi carrelli rispettano i criteri europei di stage V. Dal punto di vista meccanico sono dotati di tecnologia idrostatica, che consente un’efficace movimentazione contenendo i consumi di energia. Dal punto di vista dell’ergonomia, il tetto panoramico è stato ampliato del 25%, e ulteriormente abbassato il cruscotto per aumentare la visibilità generale. I nuovi VFG sono dotati di tecnologia telematica, con la quale l’utente può controllare tutta l’operatività dei carrelli.
Le principali novità sul fronte delle batterie agli ioni di litio
La principale novità che vede la luce in questa occasione è il controbilanciato EFG P30i, “nativamente” agli ioni di litio, con batterie ad alta potenza: 96 V. Questa nuova soluzione, presentata in anteprima ma non disponibile sul mercato prima della fine del 2021, sarà il ponte naturale fra diesel ed elettrico: le sue prestazioni saranno assolutamente analoghe a quelle dei veicoli a motore. Il tutto grazie ad una progettazione completamente rinnovata. Le batterie agli ioni di litio sono posizionate in due vani separati: in questo modo lo spazio per le gambe è raddoppiato e anche la visibilità è decisamente aumentata. Le batterie sono riscaldate, in modo da non perdere in prestazioni durante i mesi invernali.
Il veicolo è progettato per utilizzi gravosi e prevalentemente per esterni; anche gli pneumatici sono scelti per l’uso in esterno. Il veicolo è dotato di due motori elettrici, alimentati da due moduli batteria da 25 kWh ciascuno, che consentono al carrello di coprire fino a tre turni di lavoro. Anche la presa di ricarica è ridisegnata e ottimizzata per semplificare le attività di ricarica, che può avvenire anche all’esterno.
Il nuovo concetto prende il meglio dei due mondi: la sua velocità di sollevamento supera del 25% quella dei classici carrelli controbilanciati elettrici; anche la capacità di andare in salita è aumentata di un terzo rispetto alla media degli elettrici. Le batterie agli ioni di litio inoltre hanno consentito ai progettisti di gestire il peso in modo completamente diverso rispetto ai normali carrelli elettrici, condizionati dalla forma della batteria. Questo aumenta l’agilità del carrello, riducendo nel contempo il consumo di energia.
Oltre allo spazio interno che è letteralmente raddoppiato, grazie alla forma delle batterie, anche la visibilità esterna è stata migliorata: con effetti positivi sulla sicurezza del lavoro. Un passo importante, dunque, sulla via di una logistica ad emissioni zero, sulla quale Jungheinrich è fermamente impegnata. Se calcoliamo tutta la sua vita utile, il nuovo carrello consentirà di risparmiare circa il 52% di CO2 rispetto a un normale carrello a combustione interna, considerando l’attuale mix energetico europeo e tenendo conto della maggior energia richiesta per la sua produzione.
Le batterie agli ioni di litio scelte da Jungheinrich, infine, sono in particolare del tipo litio-ferro-fosfato, dunque non richiedono la presenza di cobalto e non confliggono con altre industrie che fanno uso di batterie di nuova generazione, riducendo i rischi connessi agli approvvigionamenti.
Questo dunque il futuro: non dovremo usare più i carrelli a combustione interna. Dunque – chiedono dal pubblico – i carrelli VFG presentati in precedenza, potrebbero essere gli ultimi che Jungheinrich propone con questo tipo di motori? «Sì» è la risposta di Christian Erlach.
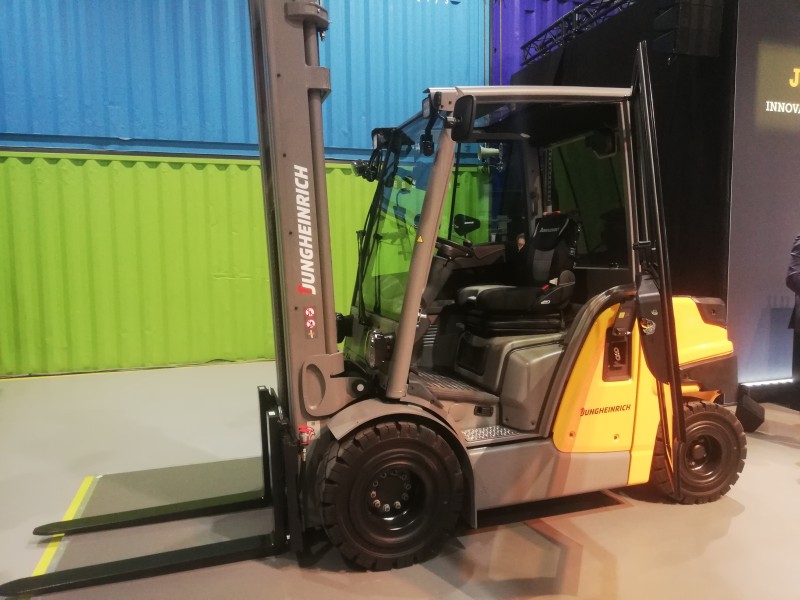
L’infrastruttura di ricarica e lo stoccaggio di energia
I carrelli con batterie agli ioni di litio possono essere caricati in tempi brevissimi, soprattutto con i nuovi caricabatterie che Jungheinrich ha messo a punto per queste soluzioni. Si tratta del nuovo sistema SLH 4001, che può essere utilizzato anche all’aperto e fornisce una potenza che va da 17 a 34 kwh; è in grado di ripristinare il 50% di carica in circa 45 minuti. Tipicamente, il tempo di una pausa pranzo.
Ma come faremo a gestire l’energia del sito in modo che sia sufficiente per un prelievo contemporaneo di energia ad alta frequenza? Per esempio immaginando una pausa pranzo in cui, esempio, dieci carrelli accedano al biberonaggio, determinando dunque un picco nei consumi, che aumenterebbe i costi dell’energia in bolletta? Ce lo spiega Michael von Forstner, presentando il nuovo caricabatterie nell’ambito di un sistema completo di gestione dell’energia, che comprende non solo una wallbox alternativa, ma anche e soprattutto nuove soluzioni di storage, sempre utilizzabili anche all’esterno.
L’esempio riportato è quello di un magazzino Ceva Logistics in Olanda, il cui tetto è coperto di pannelli solari. In questo caso, l’energia raccolta dai pannelli viene immagazzinata nelle power bank, che conservano l’energia pronte per erogarla, quando necessaria, ai carrelli. Questo dunque intende offrire Jungheinrich: soluzioni complete di gestione dell’energia, che partono dalla consulenza e analizzano fonti e consumi, in modo da mettere insieme la rete elettrica, l’impianto fotovoltaico, le batterie da alimentare (sia sui carrelli che come stoccaggio aggiuntivo) e le richieste di energia da parte dei carrelli.
Ma il fronte elettrico per Jungheinrich non finisce qui: Philipp Tielmann presenta anche la nuova soluzione Powertrain, che consentirà di fornire nuovi veicoli elettrici nel campo dell’agricoltura, del movimento terra e delle costruzioni, quali trattorini, elevatori, piccole scavatrici. Una serie di nuove macchine progettate per portare i benefici dell’elettrico anche nel mondo agricolo, oggi ancora totalmente dominato dalle motorizzazioni tradizionali.
I carrelli con batterie agli ioni di litio possono essere caricati in tempi brevissimi, soprattutto con i nuovi caricabatterie che Jungheinrich ha messo a punto per queste soluzioni. Si tratta del nuovo sistema SLH 4001, che può essere utilizzato anche all’aperto e fornisce una potenza che va da 17 a 34 kwh; è in grado di ripristinare il 50% di carica in circa 45 minuti. Tipicamente, il tempo di una pausa pranzo.
Ma come faremo a gestire l’energia del sito in modo che sia sufficiente per un prelievo contemporaneo di energia ad alta frequenza? Per esempio immaginando una pausa pranzo in cui, esempio, dieci carrelli accedano al biberonaggio, determinando dunque un picco nei consumi, che aumenterebbe i costi dell’energia in bolletta? Ce lo spiega Michael von Forstner, presentando il nuovo caricabatterie nell’ambito di un sistema completo di gestione dell’energia, che comprende non solo una wallbox alternativa, ma anche e soprattutto nuove soluzioni di storage, sempre utilizzabili anche all’esterno.
L’esempio riportato è quello di un magazzino Ceva Logistics in Olanda, il cui tetto è coperto di pannelli solari. In questo caso, l’energia raccolta dai pannelli viene immagazzinata nelle power bank, che conservano l’energia pronte per erogarla, quando necessaria, ai carrelli. Questo dunque intende offrire Jungheinrich: soluzioni complete di gestione dell’energia, che partono dalla consulenza e analizzano fonti e consumi, in modo da mettere insieme la rete elettrica, l’impianto fotovoltaico, le batterie da alimentare (sia sui carrelli che come stoccaggio aggiuntivo) e le richieste di energia da parte dei carrelli.
Ma il fronte elettrico per Jungheinrich non finisce qui: Philipp Tielmann presenta anche la nuova soluzione Powertrain, che consentirà di fornire nuovi veicoli elettrici nel campo dell’agricoltura, del movimento terra e delle costruzioni, quali trattorini, elevatori, piccole scavatrici. Una serie di nuove macchine progettate per portare i benefici dell’elettrico anche nel mondo agricolo, oggi ancora totalmente dominato dalle motorizzazioni tradizionali.
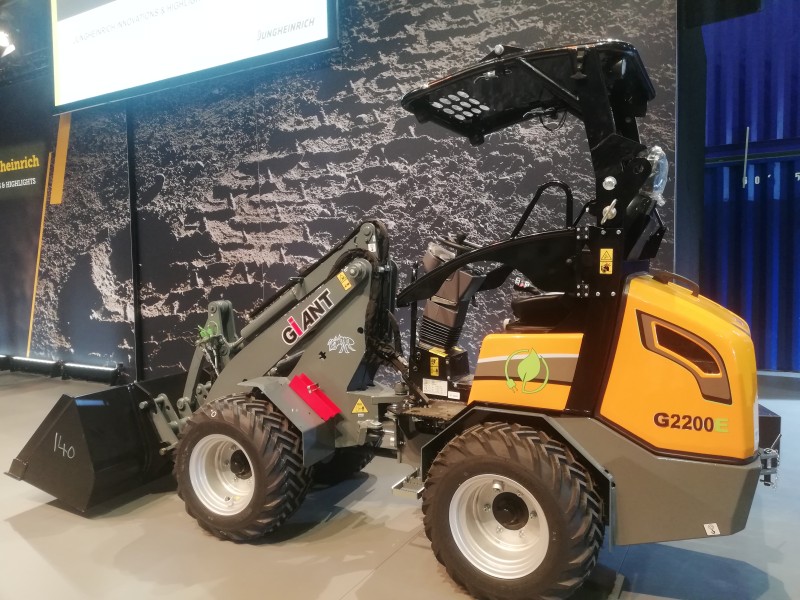
Nuove soluzioni per un magazzino più efficiente
Fra le altre novità presentate nella stessa occasione, vediamo anche la soluzione addedVIEW di scansione intelligente sulle forche, presentata da Felix Riesenhuber. Si tratta di uno scanner intelligente posizionato sulle forche, che consente di effettuare una scansione su tutta l’area di carico della merce, facendo coincidere il piano delle informazioni fisiche con quello digitale. Grazie alla fotocamera, le immagini diventano informazioni ed entrano direttamente nel sistema WMS, attraverso la Jungheinrich Logistics Interface. Così facendo è possibile verificare la corrispondenza fra codice del pallet e codice della locazione: confrontando in tempo reale i due codici aumenta l'affidabilità del processo e la velocità delle operazioni di stoccaggio e di prelievo. Con questo sistema infatti si evita uno dei più classici errori della movimentazione, in cui le merci vengono stoccate nello scomparto sbagliato ma vengono confermate come correttamente stoccate. Anche in fase di prelievo, la fotocamera digitale impedisce il prelievo di pallet sbagliati nello scaffale.
Non mancano le novità in tema di AGV, con il nuovo ERC 213a per la movimentazione autonoma di pallet, e la soluzione PH-AGV sviluppata in collaborazione con il produttore DMG MORI. Il sistema di trasporto senza conducente PH-AGV è basato su un veicolo Jungheinrich EKS 215a, e consente il carico e scarico automatico dei pallet degli utensili destinati alla produzione sulle macchine DMG MORI. Il sistema di movimentazione automatica dei pallet utilizza una tecnologia di navigazione laser molto precisa e con questa si muove liberamente nell’area di produzione, dove si allinea dolcemente con le macchine. Il nuovo sistema velocizza il flusso dei materiali e abilita processi produttivi più flessibili e più efficienti.
Altre novità, in breve, sono il caricabatterie da bordo per il carrello ETV 216i con batterie agli ioni di litio, che consente a questo veicolo di ricaricarsi ovunque, con una qualsiasi presa da 400V – 16 A; e la nuova piattaforma EKS di commissionatori verticali, il nuovo commissionatore ERC 216zi con batteria agli ioni di litio integrata e il transpallet/stoccatore EJD 222.
Tutte le novità qui descritte saranno presentate alla prossima edizione di LogiMAT, che si terrà a Stoccarda dal 10 al 12 marzo 2020, in uno spazio di oltre mille metri quadrati (stand B05, pad. 9). Per informazioni: www.logimat-messe.de
Fra le altre novità presentate nella stessa occasione, vediamo anche la soluzione addedVIEW di scansione intelligente sulle forche, presentata da Felix Riesenhuber. Si tratta di uno scanner intelligente posizionato sulle forche, che consente di effettuare una scansione su tutta l’area di carico della merce, facendo coincidere il piano delle informazioni fisiche con quello digitale. Grazie alla fotocamera, le immagini diventano informazioni ed entrano direttamente nel sistema WMS, attraverso la Jungheinrich Logistics Interface. Così facendo è possibile verificare la corrispondenza fra codice del pallet e codice della locazione: confrontando in tempo reale i due codici aumenta l'affidabilità del processo e la velocità delle operazioni di stoccaggio e di prelievo. Con questo sistema infatti si evita uno dei più classici errori della movimentazione, in cui le merci vengono stoccate nello scomparto sbagliato ma vengono confermate come correttamente stoccate. Anche in fase di prelievo, la fotocamera digitale impedisce il prelievo di pallet sbagliati nello scaffale.
Non mancano le novità in tema di AGV, con il nuovo ERC 213a per la movimentazione autonoma di pallet, e la soluzione PH-AGV sviluppata in collaborazione con il produttore DMG MORI. Il sistema di trasporto senza conducente PH-AGV è basato su un veicolo Jungheinrich EKS 215a, e consente il carico e scarico automatico dei pallet degli utensili destinati alla produzione sulle macchine DMG MORI. Il sistema di movimentazione automatica dei pallet utilizza una tecnologia di navigazione laser molto precisa e con questa si muove liberamente nell’area di produzione, dove si allinea dolcemente con le macchine. Il nuovo sistema velocizza il flusso dei materiali e abilita processi produttivi più flessibili e più efficienti.
Altre novità, in breve, sono il caricabatterie da bordo per il carrello ETV 216i con batterie agli ioni di litio, che consente a questo veicolo di ricaricarsi ovunque, con una qualsiasi presa da 400V – 16 A; e la nuova piattaforma EKS di commissionatori verticali, il nuovo commissionatore ERC 216zi con batteria agli ioni di litio integrata e il transpallet/stoccatore EJD 222.
Tutte le novità qui descritte saranno presentate alla prossima edizione di LogiMAT, che si terrà a Stoccarda dal 10 al 12 marzo 2020, in uno spazio di oltre mille metri quadrati (stand B05, pad. 9). Per informazioni: www.logimat-messe.de