11-02-2021
I robot mobili LD di Omron vengono utilizzati in combinazione con le soluzioni di EM Technologies, partner di Omron, presso la sede di Philips Austria GmbH a Klagenfurt, Austria, dove si producono, tra gli altri prodotti, oltre 23 milioni di elementi di taglio lineari per regolabarba e tagliacapelli ogni anno.
I regolabarba sono dotati di tecnologia di sollevamento e taglio: i peli della barba vengono prima sollevati con l'aiuto di speciali accessori di rifinitura e poi tagliati in modo uniforme grazie alle doppie lame in acciaio inossidabile. Il trasporto di questi elementi di taglio è stato effettuato per molti anni dagli operatori dei macchinari. Si trattava di un processo inefficiente e dispendioso in termini di tempo che richiedeva di essere automatizzato per ridurre il carico di lavoro dei dipendenti e ottimizzare l'efficienza complessiva delle apparecchiature (OEE). In questo modo i dipendenti avrebbero avuto più tempo per mettere a frutto le loro competenze in altre attività più creative e impegnative.
I regolabarba sono dotati di tecnologia di sollevamento e taglio: i peli della barba vengono prima sollevati con l'aiuto di speciali accessori di rifinitura e poi tagliati in modo uniforme grazie alle doppie lame in acciaio inossidabile. Il trasporto di questi elementi di taglio è stato effettuato per molti anni dagli operatori dei macchinari. Si trattava di un processo inefficiente e dispendioso in termini di tempo che richiedeva di essere automatizzato per ridurre il carico di lavoro dei dipendenti e ottimizzare l'efficienza complessiva delle apparecchiature (OEE). In questo modo i dipendenti avrebbero avuto più tempo per mettere a frutto le loro competenze in altre attività più creative e impegnative.
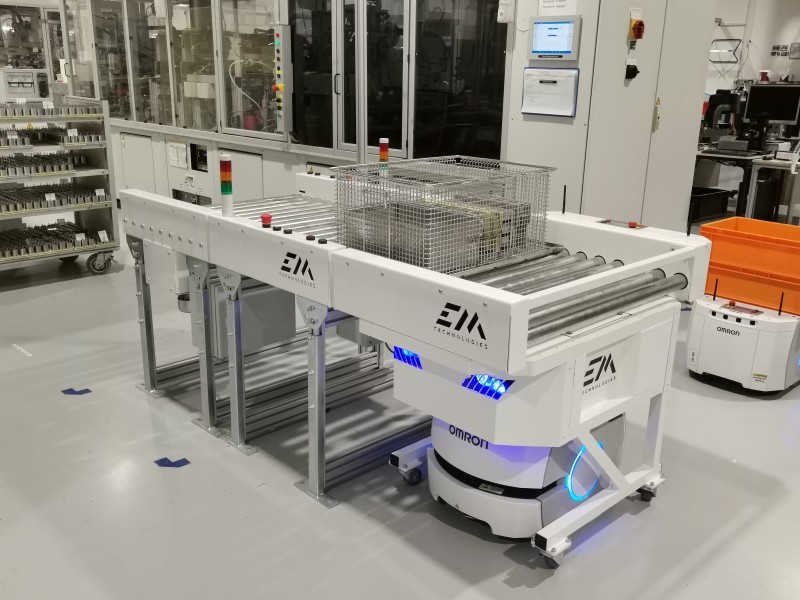
Nella scelta dei robot adatti, il team di progetto ha messo a confronto diversi fornitori, ma la scelta è presto ricaduta su Omron, i cui robot consentono facilità d'uso, velocità di trasporto relativamente elevate ed affidabilità funzionale all'interno di spazi ristretti. Oggi i robot trasportano da 500 a 1.000 elementi di taglio per contenitore.
Ogni AMR può trasportare fino a dieci contenitori e sono presenti 10.000 elementi con un peso totale compreso tra 60 e 70 kg. I robot Jaqueline, Chiara e Sepp si mettono in viaggio ogni mezz'ora. Un singolo viaggio di andata e ritorno copre circa 400 metri. In futuro, l'obiettivo è quello di trasportare materiali notevolmente più pesanti tramite robot mobili per ridurre ulteriormente il carico di lavoro dei dipendenti. Ci sono altri effetti positivi che il team di progetto non aveva mai considerato prima. Ad esempio, la migliore qualità delle parti trasportate. Il flusso di materiali avveniva in maniera disarticolata e ciò causava danni al prodotto su carrelli di trasporto fin troppo compatti. Ora che il flusso di materiali è continuo, vengono effettuati più viaggi, ma gli articoli vengono maneggiati più delicatamente. I danni da trasporto sono solo un ricordo del passato. Mentre la terza unità è in carica, ci sono sempre due robot in movimento.
Oltre al miglioramento del 3% dei valori OEE delle linee di assemblaggio grazie alla fornitura automatica, il team di progetto Philips ha riscontrato altri effetti positivi. L'azienda risparmia fino a 500 contenitori grazie al trasporto continuo di materiali. Se in precedenza il processo di lavorazione (WIP) richiedeva diversi giorni, ora potrebbe essere ridotto a poche ore grazie alla fornitura continua automatizzata di materiali.
Prospettiva: i robot mobili diventeranno sempre più intelligenti. Nella fase successiva, un AMR verrà integrato attivamente nel processo di produzione in collaborazione con i partner Omron. Oltre alle funzioni di trasporto, il robot mobile può anche eseguire l'attivazione indipendente dei sistemi, completare le fasi del processo e occuparsi delle prenotazioni di ordini tramite i codici QR. Inoltre, sono previste prenotazioni completamente automatiche nel sistema SAP. L'AMR è in grado di comunicare in maniera indipendente con la macchina.
Ogni AMR può trasportare fino a dieci contenitori e sono presenti 10.000 elementi con un peso totale compreso tra 60 e 70 kg. I robot Jaqueline, Chiara e Sepp si mettono in viaggio ogni mezz'ora. Un singolo viaggio di andata e ritorno copre circa 400 metri. In futuro, l'obiettivo è quello di trasportare materiali notevolmente più pesanti tramite robot mobili per ridurre ulteriormente il carico di lavoro dei dipendenti. Ci sono altri effetti positivi che il team di progetto non aveva mai considerato prima. Ad esempio, la migliore qualità delle parti trasportate. Il flusso di materiali avveniva in maniera disarticolata e ciò causava danni al prodotto su carrelli di trasporto fin troppo compatti. Ora che il flusso di materiali è continuo, vengono effettuati più viaggi, ma gli articoli vengono maneggiati più delicatamente. I danni da trasporto sono solo un ricordo del passato. Mentre la terza unità è in carica, ci sono sempre due robot in movimento.
Oltre al miglioramento del 3% dei valori OEE delle linee di assemblaggio grazie alla fornitura automatica, il team di progetto Philips ha riscontrato altri effetti positivi. L'azienda risparmia fino a 500 contenitori grazie al trasporto continuo di materiali. Se in precedenza il processo di lavorazione (WIP) richiedeva diversi giorni, ora potrebbe essere ridotto a poche ore grazie alla fornitura continua automatizzata di materiali.
Prospettiva: i robot mobili diventeranno sempre più intelligenti. Nella fase successiva, un AMR verrà integrato attivamente nel processo di produzione in collaborazione con i partner Omron. Oltre alle funzioni di trasporto, il robot mobile può anche eseguire l'attivazione indipendente dei sistemi, completare le fasi del processo e occuparsi delle prenotazioni di ordini tramite i codici QR. Inoltre, sono previste prenotazioni completamente automatiche nel sistema SAP. L'AMR è in grado di comunicare in maniera indipendente con la macchina.
Automazione
- Digital transformation
- elettronica & high tech
- magazzino
- movimentazione
- Robotica
- stoccaggio
22/06/2015
17/11/2015
03/03/2016
02/02/2016
11/05/2016