16-10-2023
La maggior parte degli impianti logistici è ancora gestita manualmente. Le persone impilano le merci sugli scaffali, le rimuovono e le imballano. Questo comporta un'immensa quantità di lavoro che non solo rallenta i processi, ma li rende anche più costosi. La carenza di personale qualificato fa lievitare i costi, sempre che si riesca a trovare manodopera sufficiente.
Inoltre, episodi pandemici hanno dimostrato quanto sia complesso e quindi vulnerabile un impianto logistico: la mancanza di personale, unita al rapido aumento del carico di lavoro, dopo che i consumatori di tutto il mondo hanno dovuto passare quasi completamente agli acquisti online, sono state la goccia che ha fatto traboccare il vaso.
Infine, i costi di prelievo rappresentano oggi il principale fattore di costo del magazzino e della distribuzione, nonché i costi logistici complessivi delle aziende di produzione e distribuzione.
Da studi di settore, i costi logistici rappresentano fino al 30% del fatturato di un'azienda. A sua volta, il 70% dei costi logistici può essere attribuito ai costi di magazzino e di distribuzione, in cui i costi di commissioning superano di gran lunga la quota maggiore, arrivando fino al 70%. (source: TUM fml; diagram modified from Spee, 2005, p. 3)
Oggi, molti processi possono già essere semplificati, grazie alla digitalizzazione e all'automazione. Questo non solo rende gli impianti logistici più efficienti, ma anche significativamente più immuni alle crisi: I robot possono essere impiegati 24 ore su 24, riducendo la pressione sul personale e sui processi. I veicoli a guida automatica (AGV) o i robot mobili autonomi (AMR) sono già oggi utilizzati in molti magazzini e rappresentano una serie di soluzioni di automazione che svilupperanno il loro potenziale solo nei prossimi anni.
Il raggiungimento di un magazzino completamente automatizzato è ancora in fase di sviluppo, ma da non molto sono apparse nuovissime ed avanzate possibilità di miglioramento grazie all'utilizzo di soluzioni che applicano algoritmi di intelligenza artificiale. Vediamo di capirne i vantaggi grazie ad alcuni esempi.
Inoltre, episodi pandemici hanno dimostrato quanto sia complesso e quindi vulnerabile un impianto logistico: la mancanza di personale, unita al rapido aumento del carico di lavoro, dopo che i consumatori di tutto il mondo hanno dovuto passare quasi completamente agli acquisti online, sono state la goccia che ha fatto traboccare il vaso.
Infine, i costi di prelievo rappresentano oggi il principale fattore di costo del magazzino e della distribuzione, nonché i costi logistici complessivi delle aziende di produzione e distribuzione.
Da studi di settore, i costi logistici rappresentano fino al 30% del fatturato di un'azienda. A sua volta, il 70% dei costi logistici può essere attribuito ai costi di magazzino e di distribuzione, in cui i costi di commissioning superano di gran lunga la quota maggiore, arrivando fino al 70%. (source: TUM fml; diagram modified from Spee, 2005, p. 3)
Oggi, molti processi possono già essere semplificati, grazie alla digitalizzazione e all'automazione. Questo non solo rende gli impianti logistici più efficienti, ma anche significativamente più immuni alle crisi: I robot possono essere impiegati 24 ore su 24, riducendo la pressione sul personale e sui processi. I veicoli a guida automatica (AGV) o i robot mobili autonomi (AMR) sono già oggi utilizzati in molti magazzini e rappresentano una serie di soluzioni di automazione che svilupperanno il loro potenziale solo nei prossimi anni.
Il raggiungimento di un magazzino completamente automatizzato è ancora in fase di sviluppo, ma da non molto sono apparse nuovissime ed avanzate possibilità di miglioramento grazie all'utilizzo di soluzioni che applicano algoritmi di intelligenza artificiale. Vediamo di capirne i vantaggi grazie ad alcuni esempi.
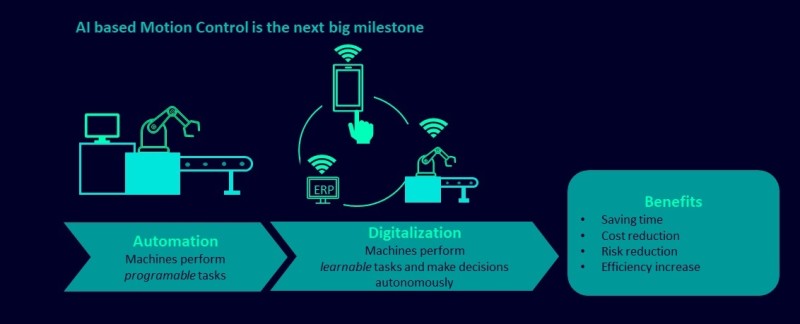
Robot abilitati all'intelligenza artificiale
Se da una parte le strategie di automazione tradizionali raggiungono i loro limiti quando i parametri cambiano in modo imprevedibile durante il funzionamento o quando un problema è troppo complesso per essere affrontato sulla base di regole definite, dall’altra lo sviluppo che sta avendo l’e-commerce sta spingendo alcuni cambiamenti nel prelievo di articoli, oggi per lo più manuale o attrezzato con sistemi di automazione tradizionale. In questo contesto un sistema robotico standard è in grado di determinare in modo indipendente pose di presa robuste per ogni oggetto durante il runtime, per poi eseguire la presa senza collisioni avendo una chiara mappatura predefinita della tipologia degli oggetti da manipolare.
Tuttavia, quando alla stazione di prelievo arrivano oggetti molto diversi tra loro, cosa che accade di frequente, è ancora necessaria la flessibilità umana, in particolare la flessibilità cognitiva per afferrare intuitivamente gli oggetti. La manipolazione affidabile di oggetti di forme e dimensioni molto diverse è uno dei problemi di automazione più impegnativi da risolvere e richiede una nuova generazione di sistemi flessibili, intelligenti e autonomi.
Sistemi robotizzati a sei assi consentono già di afferrare gli oggetti nello spazio 3D mentre sistemi di visione permettono già di riconoscere gli oggetti. Quindi è davvero necessaria l’Intelligenza artificiale? Finora i sistemi sono stati limitata alla ricerca di oggetti pre-addestrati e quindi noti, per poi afferrarli utilizzando punti di presa predeterminati: i recenti progressi nella ricerca sull'intelligenza artificiale e sulla robotica rendono possibile l'automazione di processi non standard.
Dal 2016, in collaborazione con l’Università Berkeley, Siemens sta lavorando per identificare la tecnologia di Deep Learning necessaria per il calcolo della posa (posizione nello spazio 3D) di oggetti sconosciuti e trasferire continuamente questi risultati in prodotti software industriali e renderli disponibili a tutti i fornitori di soluzioni robotiche.
L’obbiettivo è quello di semplificare le costose operazioni preliminari, grazie al pre-addestramento del sistema robotizzato tramite Deep Learning in modo che non sia più necessaria una lunga formazione del cliente e che il software possa risolvere in modo affidabile qualsiasi tipo di task facendo in modo che qualsiasi specialista dell'automazione sia in grado di aggiornare un robot standard a un robot di apprendimento in pochi minuti.
L'apertura di questa soluzione rende inoltre possibile l'utilizzo di componenti di diversi fornitori leader nel campo della visione artificiale, della tecnologia di presa e dei bracci robotici.
Come è possibile far coesistere tutto questo concentrato di tecnologia in un sistema di automazione in grado di garantire affidabilità ed efficienza energetica? Grazie al lavoro degli esperti Siemens queste soluzioni si integrano già ora nelle soluzioni SIMATIC Industrial Computing, SIMATIC Industrial Edge e in moduli SIMATIC S7-1500 e quindi nella filosofia della Totally Integrated Automation.
Se da una parte le strategie di automazione tradizionali raggiungono i loro limiti quando i parametri cambiano in modo imprevedibile durante il funzionamento o quando un problema è troppo complesso per essere affrontato sulla base di regole definite, dall’altra lo sviluppo che sta avendo l’e-commerce sta spingendo alcuni cambiamenti nel prelievo di articoli, oggi per lo più manuale o attrezzato con sistemi di automazione tradizionale. In questo contesto un sistema robotico standard è in grado di determinare in modo indipendente pose di presa robuste per ogni oggetto durante il runtime, per poi eseguire la presa senza collisioni avendo una chiara mappatura predefinita della tipologia degli oggetti da manipolare.
Tuttavia, quando alla stazione di prelievo arrivano oggetti molto diversi tra loro, cosa che accade di frequente, è ancora necessaria la flessibilità umana, in particolare la flessibilità cognitiva per afferrare intuitivamente gli oggetti. La manipolazione affidabile di oggetti di forme e dimensioni molto diverse è uno dei problemi di automazione più impegnativi da risolvere e richiede una nuova generazione di sistemi flessibili, intelligenti e autonomi.
Sistemi robotizzati a sei assi consentono già di afferrare gli oggetti nello spazio 3D mentre sistemi di visione permettono già di riconoscere gli oggetti. Quindi è davvero necessaria l’Intelligenza artificiale? Finora i sistemi sono stati limitata alla ricerca di oggetti pre-addestrati e quindi noti, per poi afferrarli utilizzando punti di presa predeterminati: i recenti progressi nella ricerca sull'intelligenza artificiale e sulla robotica rendono possibile l'automazione di processi non standard.
Dal 2016, in collaborazione con l’Università Berkeley, Siemens sta lavorando per identificare la tecnologia di Deep Learning necessaria per il calcolo della posa (posizione nello spazio 3D) di oggetti sconosciuti e trasferire continuamente questi risultati in prodotti software industriali e renderli disponibili a tutti i fornitori di soluzioni robotiche.
L’obbiettivo è quello di semplificare le costose operazioni preliminari, grazie al pre-addestramento del sistema robotizzato tramite Deep Learning in modo che non sia più necessaria una lunga formazione del cliente e che il software possa risolvere in modo affidabile qualsiasi tipo di task facendo in modo che qualsiasi specialista dell'automazione sia in grado di aggiornare un robot standard a un robot di apprendimento in pochi minuti.
L'apertura di questa soluzione rende inoltre possibile l'utilizzo di componenti di diversi fornitori leader nel campo della visione artificiale, della tecnologia di presa e dei bracci robotici.
Come è possibile far coesistere tutto questo concentrato di tecnologia in un sistema di automazione in grado di garantire affidabilità ed efficienza energetica? Grazie al lavoro degli esperti Siemens queste soluzioni si integrano già ora nelle soluzioni SIMATIC Industrial Computing, SIMATIC Industrial Edge e in moduli SIMATIC S7-1500 e quindi nella filosofia della Totally Integrated Automation.
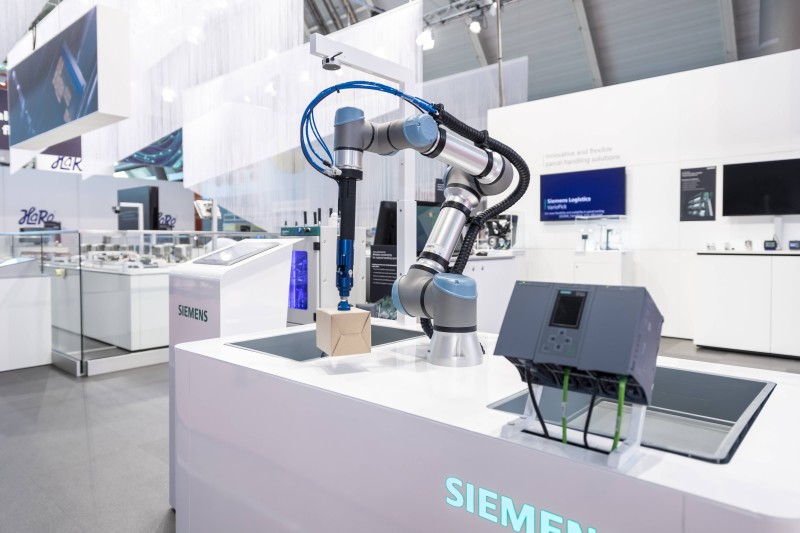
Con alcuni clienti, Siemens ha sviluppato soluzioni software in collaborazione, abilitando il deployment di modelli di AI all’interno di una macchina di automazione con tempi di inferenza minimi per adattarsi al tempo ciclo macchina.
Oggi, a guidare il robot nella ricerca della presa dell’oggetto è dunque l’AI, attraverso un processo ottimizzato in cui sono gli algoritmi a pianificare il minor numero di operazioni necessarie, utilizzando calcoli probabilistici relativi alla posizione degli oggetti da raccogliere.
Oggi, a guidare il robot nella ricerca della presa dell’oggetto è dunque l’AI, attraverso un processo ottimizzato in cui sono gli algoritmi a pianificare il minor numero di operazioni necessarie, utilizzando calcoli probabilistici relativi alla posizione degli oggetti da raccogliere.
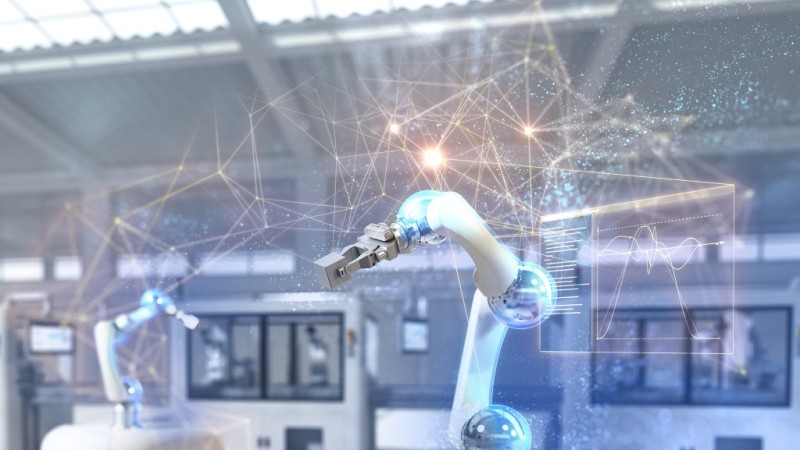
AI nei sistemi di trasporto
Nei comuni sistemi di trasporto le merci vengono spesso posizionate sul nastro di ingresso a intervalli casuali mentre sui nastri in uscita si vuole che esse siano distanziate ad intervalli regolari per permettere la corretta manipolazione e stoccaggio. Il controllore del sistema ottiene questo risultato modificando le velocità dei nastri trasportatori: la linea può essere accelerata o rallentata per garantire che la merce sia posizionata correttamente sul nastro di uscita. Lo sviluppo di un algoritmo di controllo ottimizzato per questa applicazione è un compito di programmazione molto complesso. Come risolvere? Grazie al Reinforcement Learning, è possibile addestrare un controllore con intelligenza artificiale per realizzare questo task.
Questo metodo di intelligenza artificiale funziona più o meno come la maggior parte delle persone impara ad andare in bicicletta: per tentativi ed errori, senza alcuna conoscenza della fisica di base. Il ciclista alle prime armi sperimenta la bontà della propria tecnica direttamente durante le prove di guida e quindi migliora gradualmente. Come funziona in pratica? Il sistema riceve specifica di destinazione, come ad esempio 'le merci possono essere posizionate solo nei campi di destinazione, e il sistema deve lavorare il più velocemente possibile nel processo'. L'intelligenza artificiale effettua quindi dei tentativi di controllo, inizialmente del tutto casuali e riceve un riscontro, attivato da segnali di barriera luminosa, sulla bontà di ciascun tentativo, in modo che l’algoritmo possa imparare a massimizzare le performance nel lungo periodo. Quindi, ad ogni tentativo il sistema riceve una sorta di ricompensa (reward), modifica la policy del tentativo successivo, con l’obbiettivo di massimizzare la ricompensa convergendo sulla migliore policy possibile.
Questo approccio, applicabile in diversi altri contesti, permette di realizzare un sistema di Intellgent Infeed ottimizzato, risparmiando tempo e riducendo, a regime, gli errori.
Nei comuni sistemi di trasporto le merci vengono spesso posizionate sul nastro di ingresso a intervalli casuali mentre sui nastri in uscita si vuole che esse siano distanziate ad intervalli regolari per permettere la corretta manipolazione e stoccaggio. Il controllore del sistema ottiene questo risultato modificando le velocità dei nastri trasportatori: la linea può essere accelerata o rallentata per garantire che la merce sia posizionata correttamente sul nastro di uscita. Lo sviluppo di un algoritmo di controllo ottimizzato per questa applicazione è un compito di programmazione molto complesso. Come risolvere? Grazie al Reinforcement Learning, è possibile addestrare un controllore con intelligenza artificiale per realizzare questo task.
Questo metodo di intelligenza artificiale funziona più o meno come la maggior parte delle persone impara ad andare in bicicletta: per tentativi ed errori, senza alcuna conoscenza della fisica di base. Il ciclista alle prime armi sperimenta la bontà della propria tecnica direttamente durante le prove di guida e quindi migliora gradualmente. Come funziona in pratica? Il sistema riceve specifica di destinazione, come ad esempio 'le merci possono essere posizionate solo nei campi di destinazione, e il sistema deve lavorare il più velocemente possibile nel processo'. L'intelligenza artificiale effettua quindi dei tentativi di controllo, inizialmente del tutto casuali e riceve un riscontro, attivato da segnali di barriera luminosa, sulla bontà di ciascun tentativo, in modo che l’algoritmo possa imparare a massimizzare le performance nel lungo periodo. Quindi, ad ogni tentativo il sistema riceve una sorta di ricompensa (reward), modifica la policy del tentativo successivo, con l’obbiettivo di massimizzare la ricompensa convergendo sulla migliore policy possibile.
Questo approccio, applicabile in diversi altri contesti, permette di realizzare un sistema di Intellgent Infeed ottimizzato, risparmiando tempo e riducendo, a regime, gli errori.
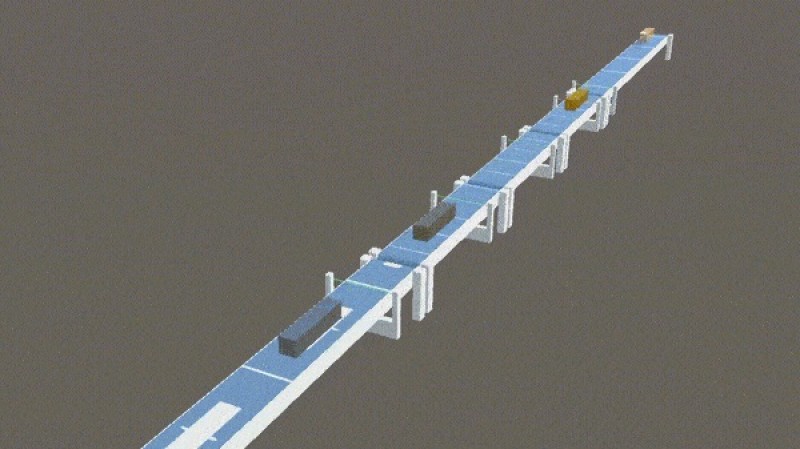
Nuove frontiere
La nuova generazione di sistemi robotizzati abilitati dall'intelligenza artificiale e l’utilizzo di moderne tecniche di autoapprendimento, cambieranno definitivamente il mercato dell'intralogistica, inaugurando un cambiamento di paradigma. Ma c’è di più.
L’uso di modelli AI comporta la necessità di verificarne l’integrità nel tempo. Per questo è necessaria l’implementazione di piattaforme aperte a bordo macchina, come Industrial Edge di Siemens, che permettono di monitorare le performance del sistema, attraverso una app industriale dedicata. Si tratta di una piattaforma in grado di colmare il divario tra local e cloud computing, portando l’IT a bordo macchina e consentendo la raccolta, lo scambio e l'analisi dei dati direttamente a livello di campo ed abilitando oltre alla verifica delle performance, anche il monitoraggio energetico e la manutenzione predittiva.
L’integrazione con l’AI permette di andare anche oltre, offrendo la possibilità di modificare il piano di smistamento senza riprogrammare l’impianto oppure inserendo nuovi prodotti in presa senza sapere quali essi siano. Come? Sembrerebbe una missione impossibile, ma in questo caso si è sfruttata la simulazione in ambiente fotorealistico, all’interno di un metaverso industriale, per ottenere dati sintetici e allenare così l’intelligenza artificiale, prima ancora di avere il pezzo a scaffale oppure nel punto di presa.
Grazie a tutte queste innovazioni sarà possibile ridurre la complessità, aumentare la competitività e diminuire la manodopera che potrà essere impiegata per compiti di maggior valore.
La nuova generazione di sistemi robotizzati abilitati dall'intelligenza artificiale e l’utilizzo di moderne tecniche di autoapprendimento, cambieranno definitivamente il mercato dell'intralogistica, inaugurando un cambiamento di paradigma. Ma c’è di più.
L’uso di modelli AI comporta la necessità di verificarne l’integrità nel tempo. Per questo è necessaria l’implementazione di piattaforme aperte a bordo macchina, come Industrial Edge di Siemens, che permettono di monitorare le performance del sistema, attraverso una app industriale dedicata. Si tratta di una piattaforma in grado di colmare il divario tra local e cloud computing, portando l’IT a bordo macchina e consentendo la raccolta, lo scambio e l'analisi dei dati direttamente a livello di campo ed abilitando oltre alla verifica delle performance, anche il monitoraggio energetico e la manutenzione predittiva.
L’integrazione con l’AI permette di andare anche oltre, offrendo la possibilità di modificare il piano di smistamento senza riprogrammare l’impianto oppure inserendo nuovi prodotti in presa senza sapere quali essi siano. Come? Sembrerebbe una missione impossibile, ma in questo caso si è sfruttata la simulazione in ambiente fotorealistico, all’interno di un metaverso industriale, per ottenere dati sintetici e allenare così l’intelligenza artificiale, prima ancora di avere il pezzo a scaffale oppure nel punto di presa.
Grazie a tutte queste innovazioni sarà possibile ridurre la complessità, aumentare la competitività e diminuire la manodopera che potrà essere impiegata per compiti di maggior valore.