23-10-2023
Nei giorni scorsi si è tenuto il webinar “Il Magazzino Evoluto” organizzato da Logistica Management in collaborazione con i partner Icam, Infor, Knapp, LCS e Manhattan Associates e moderato da Andrea Payaro, Adjunct Professor in Digital Transformation. Il pomeriggio di lavori è stato molto seguito dal pubblico, collegato in diretta streaming, e ha fornito diversi spunti di riflessione sull’ottimizzazione dello stoccaggio in minori spazi perimetrali, ma sicuramente a più alta densità di SKU che in passato.
Le presentazioni sono disponibili sul sito dell'evento, nella sezione Agenda, al seguente link (cliccare sulle frecce verdi in corrispondenza degli interventi in agenda).
Per rivedere il video, compilare il form alla fine di quest'articolo.
In apertura, Andrea Payaro ha sottolineato come la speculazione sugli acquisti e l’imprevedibilità della domanda abbiano evidenziato la necessità di una gestione efficiente degli spazi logistici. Le nuove soluzioni di storage hanno permesso, in questi anni, di aumentare la capacità di stoccaggio e ottimizzare al contempo l'utilizzo dello spazio, anche grazie all’adozione di tecniche innovative per massimizzare la capacità disponibile. «È importante passare dal concetto di “magazzino evoluto”, che sottende di essere arrivato ormai ad una fase di pieno sviluppo, al concetto di “magazzino “evolvente, ovvero che cambia continuamente per rispondere alle nuove e differenti dinamiche del mercato, grazie alla capacità di adattamento acquisita attraverso alla valorizzazione delle persone e alle soluzioni di automazione e digitalizzazione» afferma Payaro.
Le presentazioni sono disponibili sul sito dell'evento, nella sezione Agenda, al seguente link (cliccare sulle frecce verdi in corrispondenza degli interventi in agenda).
Per rivedere il video, compilare il form alla fine di quest'articolo.
In apertura, Andrea Payaro ha sottolineato come la speculazione sugli acquisti e l’imprevedibilità della domanda abbiano evidenziato la necessità di una gestione efficiente degli spazi logistici. Le nuove soluzioni di storage hanno permesso, in questi anni, di aumentare la capacità di stoccaggio e ottimizzare al contempo l'utilizzo dello spazio, anche grazie all’adozione di tecniche innovative per massimizzare la capacità disponibile. «È importante passare dal concetto di “magazzino evoluto”, che sottende di essere arrivato ormai ad una fase di pieno sviluppo, al concetto di “magazzino “evolvente, ovvero che cambia continuamente per rispondere alle nuove e differenti dinamiche del mercato, grazie alla capacità di adattamento acquisita attraverso alla valorizzazione delle persone e alle soluzioni di automazione e digitalizzazione» afferma Payaro.
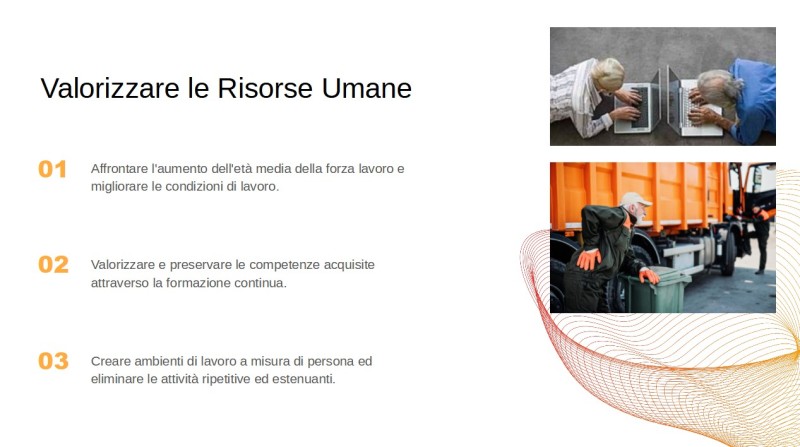
Automazione e Collaborazione
Secondo Elisa Birelli, Retail & City Logistics Manager di Icam, i driver del magazzino del futuro sono flessibilità, automazione e integrazione. Solo grazie alla commistione di queste tre leve le aziende, infatti, sono in grado di trasformare le attuali sfide di mercato, tra cui la volatilità, la complessità e l’inefficienza dei processi, in vantaggi per far evolvere il loro business. Birelli si è poi soffermata sull’ottimizzazione di tre passaggi chiave del processo logistico (logistica inbound, order picking e reverse logistics) attraverso l’adozione dei magazzini automatici di Icam che permettono un’alta densità di stoccaggio e un’elevata flessibilità operativa, adattandosi facilmente a qualsiasi contesto, grazie anche all’integrazione con tutte le piattaforme di terze parti.
Lucio Morini, Supply Chain Manager Gabbiano S.p.A., ha poi portato la propria testimonianza sull’adozione dei magazzini verticali Silo Plus di Icam per migliorare l’order picking. Nel 2021, infatti, con l’obiettivo di incrementare il pick rate orario riducendo le percorrenze degli operatori, garantire maggiore protezione agli articoli stoccati e, al contempo, ottimizzare lo spazio disponibile nell’hub logistico di Mantova, l’azienda decide di automatizzare le attività di stoccaggio e picking di questa tipologia di referenze installando strategicamente due magazzini automatici verticali SILO Plus nell’area di fine linea del magazzino a gravità.
Alti più di 7 metri e composti da 2 colonne di stoccaggio con 2 baie di prelievo e deposito affiancate entrambe dotate di IRIDE, consentono di preparare fino a 6 ordini contemporaneamente. oggi, lo stesso operatore è in grado di preparare 6 ordini contemporaneamente ed effettuare circa 210 prelievi all’ora a differenza prima quando riusciva a preparare un solo ordine alla volta ed effettuare circa 148 prelievi all’ora. Ogni giorno, in media, vengono evase 800 - 1.200 confezioni, che equivalgono a circa 210 prelievi all’ora per operatore. Infine, all’interno dei SILO Plus viene gestito un numero di referenze per le quali, in alternativa, Gabbiano avrebbe dovuto aggiungere 30 m di pedana con corsia bifronte nell’attuale magazzino a gravità o 52 metri nel caso di pedana con corsia mono fronte.
Secondo Elisa Birelli, Retail & City Logistics Manager di Icam, i driver del magazzino del futuro sono flessibilità, automazione e integrazione. Solo grazie alla commistione di queste tre leve le aziende, infatti, sono in grado di trasformare le attuali sfide di mercato, tra cui la volatilità, la complessità e l’inefficienza dei processi, in vantaggi per far evolvere il loro business. Birelli si è poi soffermata sull’ottimizzazione di tre passaggi chiave del processo logistico (logistica inbound, order picking e reverse logistics) attraverso l’adozione dei magazzini automatici di Icam che permettono un’alta densità di stoccaggio e un’elevata flessibilità operativa, adattandosi facilmente a qualsiasi contesto, grazie anche all’integrazione con tutte le piattaforme di terze parti.
Lucio Morini, Supply Chain Manager Gabbiano S.p.A., ha poi portato la propria testimonianza sull’adozione dei magazzini verticali Silo Plus di Icam per migliorare l’order picking. Nel 2021, infatti, con l’obiettivo di incrementare il pick rate orario riducendo le percorrenze degli operatori, garantire maggiore protezione agli articoli stoccati e, al contempo, ottimizzare lo spazio disponibile nell’hub logistico di Mantova, l’azienda decide di automatizzare le attività di stoccaggio e picking di questa tipologia di referenze installando strategicamente due magazzini automatici verticali SILO Plus nell’area di fine linea del magazzino a gravità.
Alti più di 7 metri e composti da 2 colonne di stoccaggio con 2 baie di prelievo e deposito affiancate entrambe dotate di IRIDE, consentono di preparare fino a 6 ordini contemporaneamente. oggi, lo stesso operatore è in grado di preparare 6 ordini contemporaneamente ed effettuare circa 210 prelievi all’ora a differenza prima quando riusciva a preparare un solo ordine alla volta ed effettuare circa 148 prelievi all’ora. Ogni giorno, in media, vengono evase 800 - 1.200 confezioni, che equivalgono a circa 210 prelievi all’ora per operatore. Infine, all’interno dei SILO Plus viene gestito un numero di referenze per le quali, in alternativa, Gabbiano avrebbe dovuto aggiungere 30 m di pedana con corsia bifronte nell’attuale magazzino a gravità o 52 metri nel caso di pedana con corsia mono fronte.
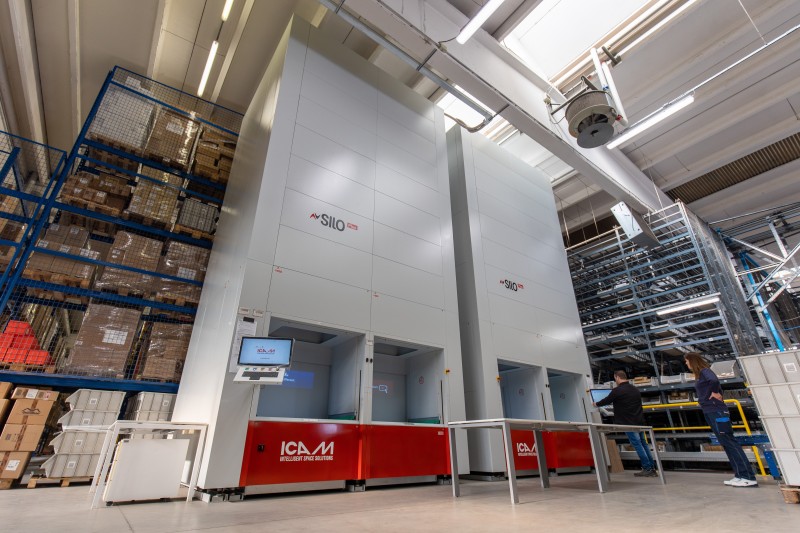
Tutto sotto controllo con il warehouse management
Con Paolo Lanzani, Senior Sales Account Manager Infor, si passa invece alle soluzione di digitalizzazione della supply chain, in particolare grazie al WMS che può aiutare le aziende a ottimizzare i processi logistici e migliorare l'efficienza e la produttività del magazzino su almeno tre fronti. «Innanzitutto offrono una migliore precisione ed efficienza, perchè i sistemi WMS automatizzano le attività di gestione del magazzino, riducendo il rischio di errori e migliorando l'efficienza dei processi. Inoltre, le aziende ottengono una riduzione dei costi, in quanto gli WMS possono aiutare a ridurre i costi di gestione del magazzino, ad esempio riducendo gli sprechi e migliorando la produttività. Infine, tali sistemi migliorano la soddisfazione dei clienti, ad esempio riducendo i tempi di consegna e migliorando la precisione degli ordini» spiega Paolo Lanzani.
Per raggiungere questi risultati è necessario automatizzare le attività di gestione del magazzino, introdurre tecnologie avanzate come l'intelligenza artificiale, l'apprendimento automatico e la robotica. Il brand premium di prodotti per la cura della pelle Clarins UK ha implementato il sistema di gestione del magazzino Infor WMS. Con l'obiettivo di creare un'infrastruttura scalabile e di migliorare sia la tracciabilità che l'accuratezza degli ordini dei clienti, Clarins aveva bisogno di abbandonare il precedente sistema di gestione del magazzino legacy. Supportando un nuovo centro di distribuzione, la soluzione cloud, basata su AWS (Amazon Web Services), ha permesso di ottenere una maggiore visibilità, migliore tracciabilità e accuratezza dell'inventario. La soluzione ha migliorato anche la gestione degli ordini e il prelievo dinamico, per una produttività ottimale. Infor ha annunciato che HAVI Group, azienda globale che innova, ottimizza e gestisce le supply chain dei principali marchi di ristorazione, ha implementato Infor WMS, soluzione di warehouse management, in ambiente cloud.
Anche Havi prevede di implementare Infor WMS in oltre 50 dei suoi centri di distribuzione in Europa e Giappone, entro la fine del 2026, con l’obiettivo di contribuire a migliorare costantemente il servizio, l'efficienza e la resilienza operativa da queste sedi. Dopo un anno di ricerca, HAVI ha scelto Infor WMS, riconoscendo i punti di forza della sua architettura tecnologica all'avanguardia, che garantisce in ogni momento i più elevati standard di sicurezza informatica, disponibilità del servizio 24 ore su 24, efficienza operativa ottimale e la sicurezza e la tracciabilità degli alimenti lungo tutta la supply chain. HAVI intende inoltre sfruttare le funzionalità avanzate di gestione delle operazioni di magazzino e di pianificazione delle risorse, che includono la visualizzazione in 3D e un approccio all'esecuzione data-driven.
Con Paolo Lanzani, Senior Sales Account Manager Infor, si passa invece alle soluzione di digitalizzazione della supply chain, in particolare grazie al WMS che può aiutare le aziende a ottimizzare i processi logistici e migliorare l'efficienza e la produttività del magazzino su almeno tre fronti. «Innanzitutto offrono una migliore precisione ed efficienza, perchè i sistemi WMS automatizzano le attività di gestione del magazzino, riducendo il rischio di errori e migliorando l'efficienza dei processi. Inoltre, le aziende ottengono una riduzione dei costi, in quanto gli WMS possono aiutare a ridurre i costi di gestione del magazzino, ad esempio riducendo gli sprechi e migliorando la produttività. Infine, tali sistemi migliorano la soddisfazione dei clienti, ad esempio riducendo i tempi di consegna e migliorando la precisione degli ordini» spiega Paolo Lanzani.
Per raggiungere questi risultati è necessario automatizzare le attività di gestione del magazzino, introdurre tecnologie avanzate come l'intelligenza artificiale, l'apprendimento automatico e la robotica. Il brand premium di prodotti per la cura della pelle Clarins UK ha implementato il sistema di gestione del magazzino Infor WMS. Con l'obiettivo di creare un'infrastruttura scalabile e di migliorare sia la tracciabilità che l'accuratezza degli ordini dei clienti, Clarins aveva bisogno di abbandonare il precedente sistema di gestione del magazzino legacy. Supportando un nuovo centro di distribuzione, la soluzione cloud, basata su AWS (Amazon Web Services), ha permesso di ottenere una maggiore visibilità, migliore tracciabilità e accuratezza dell'inventario. La soluzione ha migliorato anche la gestione degli ordini e il prelievo dinamico, per una produttività ottimale. Infor ha annunciato che HAVI Group, azienda globale che innova, ottimizza e gestisce le supply chain dei principali marchi di ristorazione, ha implementato Infor WMS, soluzione di warehouse management, in ambiente cloud.
Anche Havi prevede di implementare Infor WMS in oltre 50 dei suoi centri di distribuzione in Europa e Giappone, entro la fine del 2026, con l’obiettivo di contribuire a migliorare costantemente il servizio, l'efficienza e la resilienza operativa da queste sedi. Dopo un anno di ricerca, HAVI ha scelto Infor WMS, riconoscendo i punti di forza della sua architettura tecnologica all'avanguardia, che garantisce in ogni momento i più elevati standard di sicurezza informatica, disponibilità del servizio 24 ore su 24, efficienza operativa ottimale e la sicurezza e la tracciabilità degli alimenti lungo tutta la supply chain. HAVI intende inoltre sfruttare le funzionalità avanzate di gestione delle operazioni di magazzino e di pianificazione delle risorse, che includono la visualizzazione in 3D e un approccio all'esecuzione data-driven.
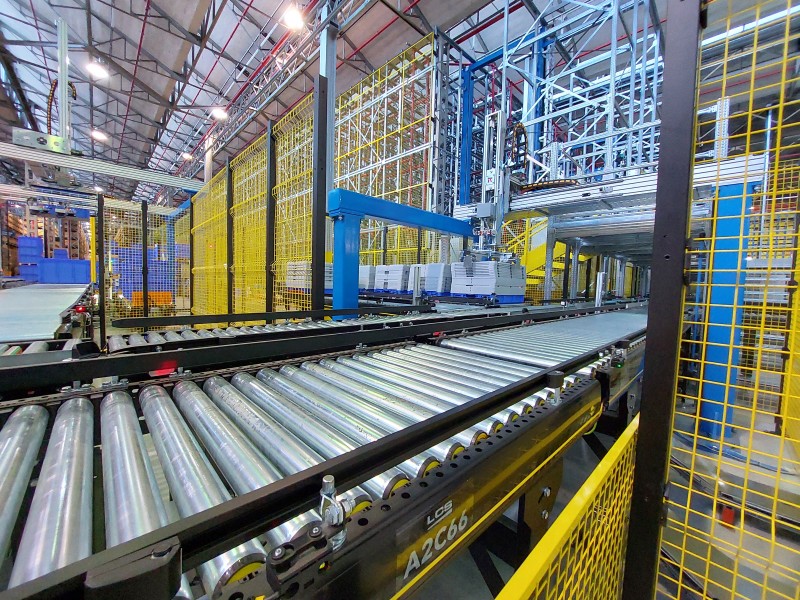
Nuovi orizzonti nel Factory Automation
Si torna a parlare di evoluzione dei sistemi di automazione con Alessandro Stea, Sales Manager, Knapp Italia, che ha percorso la storia evolutiva della propria azienda e delle tecnologie proprietarie. «L'evoluzione di Knapp - racconta Stea – non riguarda soltanto i magazzini automatici, ma anche soluzioni meno conosciute, come ad esempio le postazioni ergonomiche di assemblaggio guidate da telecamere di visione e ispezione, dotate d'Intelligenza Artificiale, che consentono agli operatori di assemblare parti meccaniche, anche estremamente complesse, come alcuni componenti automotive, ad errore zero. Questa evoluzione nelle soluzioni è stata resa possibile grazie allo sviluppo della nostra tecnologia software proprietaria, che ad oggi occupa più di 2.000 persone al nostro interno. Per fare del buon hardware, infatti, è necessario che ci sia un software in grado di integrare tutti i componenti nella maniera più fluida possibile».
Stea ha poi introdotto il caso Digmesa Polyform che, in soli quattro mesi, è riuscito ad automatizzare i processi di trasporto che alimentano le macchine di assemblaggio grazie all’adozione di un Open Shuttle. La soluzione viene infatti impiegata per portare i contenitori vuoti alle macchine per lo stampaggio a iniezione e per trasportare i pezzi finiti alla postazione successiva. L'archiviazione buffer è organizzata secondo il modello FIFO (first-in, first-out), mentre un PLC Knapp controlla completamente la soluzione senza alcun collegamento a un sistema host.
Infine, nell'ambito dell'installazione di un nuovo stabilimento per componenti di trasmissione a Kapfenberg (Austria), il cliente Pankl ha scelto la tecnologia shuttle di KNAPP per l'automazione del magazzino di minuteria con rifornimento delle postazioni di lavoro. La nuova soluzione consiste in un sistema automatizzato YLOG-Shuttle con 4.300 allocazioni, collegato a tre postazioni di lavoro e perfettamente scalabile per adattarsi alla crescita aziendale e garantisce un'elevata disponibilità.
Si torna a parlare di evoluzione dei sistemi di automazione con Alessandro Stea, Sales Manager, Knapp Italia, che ha percorso la storia evolutiva della propria azienda e delle tecnologie proprietarie. «L'evoluzione di Knapp - racconta Stea – non riguarda soltanto i magazzini automatici, ma anche soluzioni meno conosciute, come ad esempio le postazioni ergonomiche di assemblaggio guidate da telecamere di visione e ispezione, dotate d'Intelligenza Artificiale, che consentono agli operatori di assemblare parti meccaniche, anche estremamente complesse, come alcuni componenti automotive, ad errore zero. Questa evoluzione nelle soluzioni è stata resa possibile grazie allo sviluppo della nostra tecnologia software proprietaria, che ad oggi occupa più di 2.000 persone al nostro interno. Per fare del buon hardware, infatti, è necessario che ci sia un software in grado di integrare tutti i componenti nella maniera più fluida possibile».
Stea ha poi introdotto il caso Digmesa Polyform che, in soli quattro mesi, è riuscito ad automatizzare i processi di trasporto che alimentano le macchine di assemblaggio grazie all’adozione di un Open Shuttle. La soluzione viene infatti impiegata per portare i contenitori vuoti alle macchine per lo stampaggio a iniezione e per trasportare i pezzi finiti alla postazione successiva. L'archiviazione buffer è organizzata secondo il modello FIFO (first-in, first-out), mentre un PLC Knapp controlla completamente la soluzione senza alcun collegamento a un sistema host.
Infine, nell'ambito dell'installazione di un nuovo stabilimento per componenti di trasmissione a Kapfenberg (Austria), il cliente Pankl ha scelto la tecnologia shuttle di KNAPP per l'automazione del magazzino di minuteria con rifornimento delle postazioni di lavoro. La nuova soluzione consiste in un sistema automatizzato YLOG-Shuttle con 4.300 allocazioni, collegato a tre postazioni di lavoro e perfettamente scalabile per adattarsi alla crescita aziendale e garantisce un'elevata disponibilità.
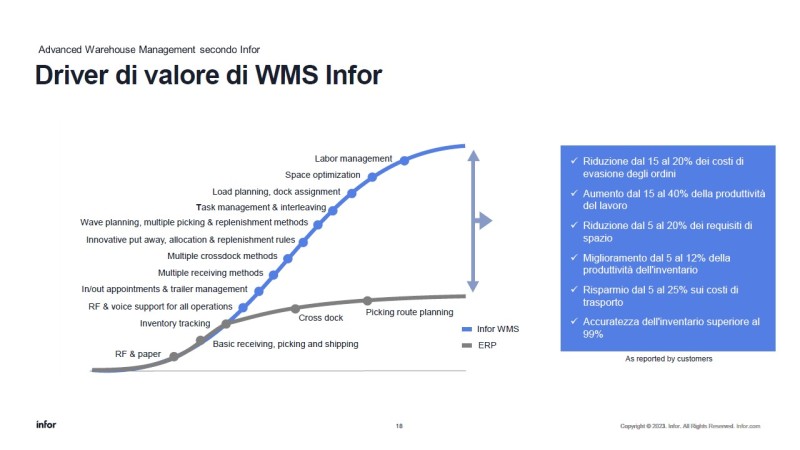
Automazione nello stoccaggio e movimentazione ricambi
Si continua a parlare di automazione con Roberto Natali, Senior Sales Engineer di LCS, che ha presentato insieme a Marco Mantello, Contract Logistics Operations Manager di Kuehne+Nagel e Federica Giacalone, Quality and Customer Service Manager di Kuehne+Nagel, il caso d’eccellenza del magazzino parti di ricambio di Iveco aTorino, gestito in outsourcing dall’operatore logistico, oggetto di più interventi di revamping finalizzati all’adeguamento delle nuove necessità di stoccaggio dovute all’aumento dei volumi. «Il magazzino automatico, dotato di 8 trasloelevatori, presenta alcune particolarità. – spiega Natali - La prima è che vengono stoccate delle casse da 600x800 mm, che hanno un peso di circa un centinaio di kg. In aggiunta, oltre al picking effettuato tramite delle baie funzionali sia per imballare in piccoli cartoni che in cartonbox, l'operatore è guidato con un sistema di put to light e di controllo del peso. Ci sono inoltre dei robot antropomorfi che depallettizzano le cassette in entrata e, in cascata, c'è un secondo robot che le chiude applicandovi un coperchio sopra, così che la merce risulti coperta e in sicurezza».
Il primo adeguamento di una certa rilevanza è stato effettuato negli anni 2008-2009, quando LCS ha “rinnovato” il software di automazione (PLC) di tutto l’impianto di trasporto cassette, il software di controllo/supervisione dell’impianto (WCS) ed il software di gestione del magazzino automatico (WMS), introducendo miglioramenti a tutti i livelli per incrementare le performance del sistema magazzino. Il secondo adeguamento/ampliamento è stato effettuato nel 2010-2011, affiancando ai 4 corridoi esistenti con lunghezza di 150 metri due nuovi corridoi con relativi trasloelevatori dotati di tre mezzi di presa cadauno. Il terzo adeguamento/ampliamento è stato effettuato nel corso del 2019 al fine di potenziare e sviluppare ulteriormente l’efficiente gestione automatica degli articoli posti in cassette e prelevata con il metodo “merce all’uomo” rispetto ad una gestione “tradizionale” con metodo “uomo alla merce”. LCS ha quindi sviluppato e implementato una soluzione integrata che consiste nell’aggiunta di 2 trasloelevatori per lo stoccaggio di cassette Odette da 600×400 mm in doppia profondità incrementando la capacità statica di stoccaggio di circa 37.500 cassette. Il collegamento tra i conveyor esistenti ed i nuovi trasloelevatori è stato realizzato tramite una nuova testata su due livelli (IN/OUT) con trasportatori a rulli e deviatori posti su soppalco a quota 5 metri di altezza.
Si continua a parlare di automazione con Roberto Natali, Senior Sales Engineer di LCS, che ha presentato insieme a Marco Mantello, Contract Logistics Operations Manager di Kuehne+Nagel e Federica Giacalone, Quality and Customer Service Manager di Kuehne+Nagel, il caso d’eccellenza del magazzino parti di ricambio di Iveco aTorino, gestito in outsourcing dall’operatore logistico, oggetto di più interventi di revamping finalizzati all’adeguamento delle nuove necessità di stoccaggio dovute all’aumento dei volumi. «Il magazzino automatico, dotato di 8 trasloelevatori, presenta alcune particolarità. – spiega Natali - La prima è che vengono stoccate delle casse da 600x800 mm, che hanno un peso di circa un centinaio di kg. In aggiunta, oltre al picking effettuato tramite delle baie funzionali sia per imballare in piccoli cartoni che in cartonbox, l'operatore è guidato con un sistema di put to light e di controllo del peso. Ci sono inoltre dei robot antropomorfi che depallettizzano le cassette in entrata e, in cascata, c'è un secondo robot che le chiude applicandovi un coperchio sopra, così che la merce risulti coperta e in sicurezza».
Il primo adeguamento di una certa rilevanza è stato effettuato negli anni 2008-2009, quando LCS ha “rinnovato” il software di automazione (PLC) di tutto l’impianto di trasporto cassette, il software di controllo/supervisione dell’impianto (WCS) ed il software di gestione del magazzino automatico (WMS), introducendo miglioramenti a tutti i livelli per incrementare le performance del sistema magazzino. Il secondo adeguamento/ampliamento è stato effettuato nel 2010-2011, affiancando ai 4 corridoi esistenti con lunghezza di 150 metri due nuovi corridoi con relativi trasloelevatori dotati di tre mezzi di presa cadauno. Il terzo adeguamento/ampliamento è stato effettuato nel corso del 2019 al fine di potenziare e sviluppare ulteriormente l’efficiente gestione automatica degli articoli posti in cassette e prelevata con il metodo “merce all’uomo” rispetto ad una gestione “tradizionale” con metodo “uomo alla merce”. LCS ha quindi sviluppato e implementato una soluzione integrata che consiste nell’aggiunta di 2 trasloelevatori per lo stoccaggio di cassette Odette da 600×400 mm in doppia profondità incrementando la capacità statica di stoccaggio di circa 37.500 cassette. Il collegamento tra i conveyor esistenti ed i nuovi trasloelevatori è stato realizzato tramite una nuova testata su due livelli (IN/OUT) con trasportatori a rulli e deviatori posti su soppalco a quota 5 metri di altezza.
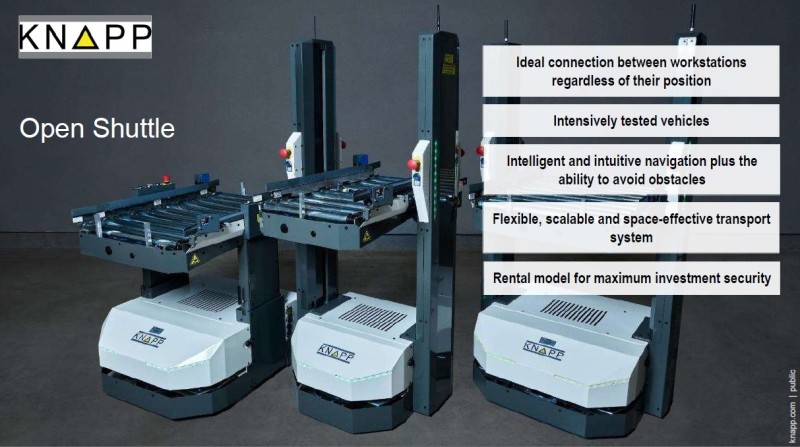
Il giusto equilibrio tra Stock, vendite e servizio
A concludere la giornata di lavori, Andrea Bertinetto Principal Consultant, Manhattan Associates, e Nicola Pianta, Principal Consultant, Manhattan Associates, che hanno presentato tutta la carica innovativa delle soluzioni di Manhattan Associates. Le recenti trasformazioni in ambito supply chain hanno influenzato significativamente le soluzione informatiche. In un contesto che si evolve e cambia nel tempo, un WMS non può fare altro che adattarsi ed evolversi a sua volta. Manhattan Active® Warehouse Management ottimizza il processo di evasione degli ordini attraverso la distribuzione, slotting, labor e automazione.
Inoltre, orchestra diverse combinazioni di robotica ed automazione, oltre che abilita ad una maggiore visibilità a livello enterprise fornendo dati utili dai ogni processo. Grazie ad un’architettura cloudnative, scalabile ed estensibile, con questa soluzione nessun upgrade sarà più necessario.
«Manhattan Active Warehouse Management è il primo sistema al mondo per la gestione del magazzino di classe enterprise nativo del cloud, in grado di unificare ogni aspetto della distribuzione e che non necessita mai di aggiornamenti. Con un'architettura interamente composta di microservizi, cambia tutto e non necessita di aggiornamenti» aggiunge Andrea Bertinetto. Questa architettura avanzata, con la sua adattabilità e facilità d'uso, rende la soluzione la scelta ideale per warehouse con livelli medi di complessità, fino ai centri di distribuzione più grandi e automatizzati del mondo.
«Le operazioni vanno oltre le semplici attività di ricevimento, preparazione e spedizione per creare un flusso continuo di prodotti e informazioni. Manhattan Active Warehouse Management rappresenta pertanto una svolta per tutte le aziende che operano in ambienti complessi, esigenti e imprevedibili. Grazie alla scienza comportamentale e alla gamification, crea esperienze più coinvolgenti e gratificanti per gli operatori» conclude Bertinetto.
A concludere la giornata di lavori, Andrea Bertinetto Principal Consultant, Manhattan Associates, e Nicola Pianta, Principal Consultant, Manhattan Associates, che hanno presentato tutta la carica innovativa delle soluzioni di Manhattan Associates. Le recenti trasformazioni in ambito supply chain hanno influenzato significativamente le soluzione informatiche. In un contesto che si evolve e cambia nel tempo, un WMS non può fare altro che adattarsi ed evolversi a sua volta. Manhattan Active® Warehouse Management ottimizza il processo di evasione degli ordini attraverso la distribuzione, slotting, labor e automazione.
Inoltre, orchestra diverse combinazioni di robotica ed automazione, oltre che abilita ad una maggiore visibilità a livello enterprise fornendo dati utili dai ogni processo. Grazie ad un’architettura cloudnative, scalabile ed estensibile, con questa soluzione nessun upgrade sarà più necessario.
«Manhattan Active Warehouse Management è il primo sistema al mondo per la gestione del magazzino di classe enterprise nativo del cloud, in grado di unificare ogni aspetto della distribuzione e che non necessita mai di aggiornamenti. Con un'architettura interamente composta di microservizi, cambia tutto e non necessita di aggiornamenti» aggiunge Andrea Bertinetto. Questa architettura avanzata, con la sua adattabilità e facilità d'uso, rende la soluzione la scelta ideale per warehouse con livelli medi di complessità, fino ai centri di distribuzione più grandi e automatizzati del mondo.
«Le operazioni vanno oltre le semplici attività di ricevimento, preparazione e spedizione per creare un flusso continuo di prodotti e informazioni. Manhattan Active Warehouse Management rappresenta pertanto una svolta per tutte le aziende che operano in ambienti complessi, esigenti e imprevedibili. Grazie alla scienza comportamentale e alla gamification, crea esperienze più coinvolgenti e gratificanti per gli operatori» conclude Bertinetto.
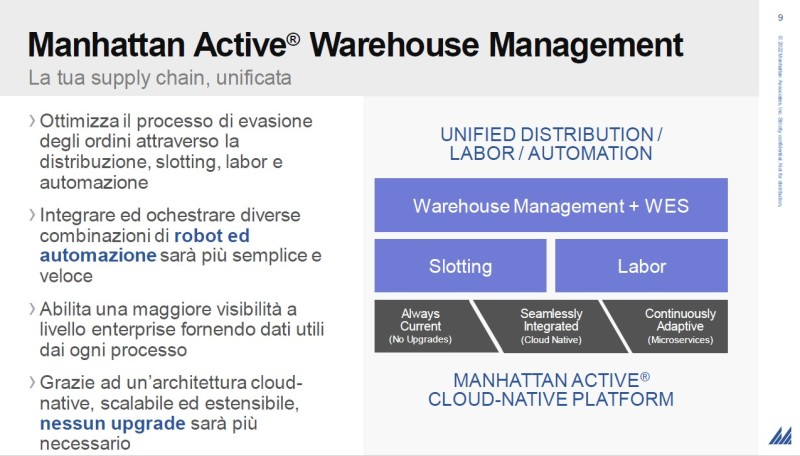