Sintesi dell’intervento di Francesco Verde, IT Transformation Manager & Project Management Director, Safilo Group, al convegno organizzato sul tema “control tower” dal Club Produzione e Tecnologia di SDA Bocconi
Per le caratteristiche del suo prodotto, Safilo si può definire in tutto e per tutto un’azienda di moda, e in quanto tale, ha un’attività specifica legata a collezioni in continuo rinnovamento. Per ciascuno dei trenta brand gestiti, infatti, vengono lanciate tre collezioni all’anno, ognuna delle quali comprende diversi modelli e, per ciascuno, diverse varianti di taglia e colore, per un totale di oltre 30 milioni di pezzi distribuiti all’anno. Ogni singola variante ha un codice diverso: di conseguenza, l’azienda si trova a gestire decine di migliaia di codici diversi ogni anno (circa 30 mila SKU). Secondo, importante elemento di complessità della supply chain Safilo, è la sofistificazione dell’industria dell’occhialeria dal punto di vista delle tecniche di produzione e di un mix di tecnologie ed artigianalità (pensando all’alta gamma del Made in Italy). Il tempo che intercorre dalla fase di completamento disegno e concept a quella della realizzazione del lotto zero, è di circa nove settimane, il tutto per mettere sul mercato prodotti fashion che verranno magari sostituiti da nuove collezioni nell’arco di pochi mesi. Una corretta pianificazione dunque è essenziale per evitare i due rischi principali: non riuscire a servire il mercato per mancanza di prodotto, o dover gestire scorte eccessive per mancanza di tempestività.
Le esigenze del prodotto fashion e le specificità produttive sono gli aspetti principali della complessità che sta dietro alla realizzazione e commercializzazione dell’occhiale; indispensabile dunque gestirla con uno strumento adeguato di pianificazione, per soddisfare al meglio le esigenze del mercato. Considerando anche che i vari prodotti vengono commercializzati mediante canali diversi che ne differenziano sostanzialmente le performance: dunque ogni responsabile commerciale per ogni singolo brand dovrà prevedere molto attentamente le diverse performance anche degli stessi prodotti ma su canali diversi. E non stiamo parlando solo di punti vendita diversi – negozi di ottica, grandi catene, distributori o rivenditori specializzati… - ma anche di caratteristiche stesse del prodotto che influenzano volumi di vendita diversa nei vari paesi. Tenuto conto di tutto questo, è fondamentale che le forze commerciali e di pianificazione siano in grado di generare, per i 9-12-15-18 mesi a venire, previsioni di vendita accurate per ciascun modello, ma anche che queste informazioni siano rese subito fruibili a chi deve produrre e distribuire.
Quali erano dunque gli obiettivi dell’azienda, alla base del progetto “control tower”? Quelli che, sostanzialmente, appartengono a qualsiasi realtà aziendale, enfatizzati però dal contesto fashion. Il miglioramento del livello di servizio al cliente (attraverso il miglioramento della disponibilità di prodotto); la riduzione dei livello di inventario e di stock lungo tutto il network con aumento dell’efficienza distributiva; la riduzione dell’obsolescenza di prodotto, figlia del punto precedente, e particolarmente dolorosa nel mondo fashion; e in generale, la riduzione delle voci di costo nel processo di fornitura ai vari nodi della rete, sia produttiva che distributiva. Si è reso necessario dunque un progetto di pianificazione integrata, capace di mettere insieme il forecast generato dalle varie regioni, la pianificazione globale, i conseguenti requirement di produzione, la pianificazione locale e quindi la distribuzione fisica; ovvero, le informazioni provenienti dalle diverse divisioni aziendali, quali Sales Planning, Global Demand Planning, Central Supply Planning, Local planning e Sales Order Fulfillment.
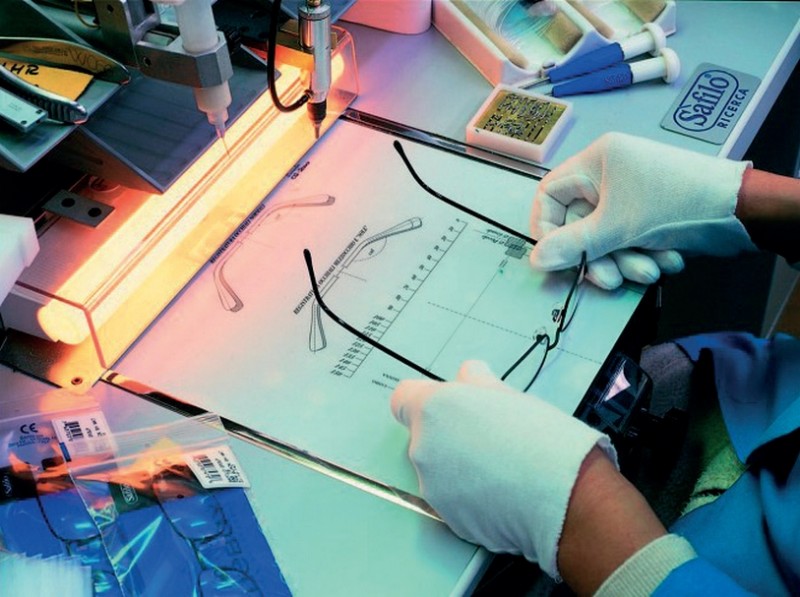
LA RETE PRODUTTIVA E DISTRIBUTIVA
I prodotti Safilo sono presenti in circa 130 paesi del mondo, tramite quaranta filiali commerciali di proprietà e un network di rappresentanti e distributori locali, grazie ai quali si raggiungono oltre 100mila punti vendita. Il Gruppo dispone di sette stabilimenti produttivi propri, di cui quattro in Italia (Longarone, Martignacco, Santa Maria di Sala e Bergamo) e tre all’estero (Slovenia, Stati Uniti e Cina). Padova, che è anche la sede centrale del gruppo, è l’hub centrale di distribuzione per tutto il mondo; da qui si alimentano i magazzini esteri, principalmente Stati Uniti (Denver), Messico, Brasile, Cina, Australia e Hong Kong.
Per quanto riguarda la produzione, i plant sono tutti interconnessi, in quanto ognuno può e deve fungere da terzista per gli altri e produrre semilavorati che dovranno essere finiti in un altro stabilimento, per poi essere reinviati al Paese di provenienza per la distribuzione finale. Alle realtà produttive di proprietà si aggiunge poi la nutrita rete dei terzisti veri e propri, che forniscono sia semilavorati che prodotti finiti, sia all’estero che in Italia. Ed è proprio questo aspetto che ha generato l’esigenza specifica di un progetto di pianificazione integrata, proprio per poter gestire in modo più efficiente le complicate interconnessioni fra i vari plant produttivi e distributivi, tenendo presente le caratteristiche del prodotto citate prima: esigenze fashion e tecnologia sofisticata. La supply chain di Safilo è stata schematizzata nella Figura 1, che ne riporta i passaggi fondamentali: Sales Planning, Demand Planning, Distribution Requirement Planning, Enterprise Supply Planning, Manufacturing & Purchasing Planning Execution, Distribution Planning e Logistics Execution. In partenza vi sono le informazioni di forecast, che nascono, tipicamente, dall’analisi del venduto. Oggi, in seguito al progetto di pianificazione integrata condotto con JDA, che ha appunto consentito di raccogliere presso un unico punto di visibilità tutte queste informazioni, il flusso informativo è gestito centralmente e nelle due direzioni, ma in uno schema classico le informazioni di previsione devono essere convogliate nella fase di Distribution and Requirement Planning, per poter pianificare l’attività degli stabilimenti, inviando loro l’ordine di produzione oppure di riordino verso i magazzini.
Con le soluzioni di JDA oggi questi dati, provenienti dalle diverse divisioni aziendali, convergono su una piattaforma unica, dove vengono elaborati consentendo di ottimizzare la produzione e la distribuzione, a ritroso, in base alle vendite e alle previsioni di vendita. In particolare, l’introduzione dell’applicativo JDA Fullfilment (DRP) ha consentito a Safilo di ottenere la visibilità totale, e in tempo reale, di ogni singolo pezzo in ogni singolo magazzino distributivo nel mondo. Di conseguenza, si può pianificare il fabbisogno necessario su ogni singolo magazzino e su ogni singolo mercato, poiché il requirement – che corrisponde a un ordine di produzione o di riordino – viene alimentato da dati costantemente aggiornati. Le assegnazioni ai singoli stabilimenti possono infatti essere pianificate centralmente, grazie a questo continuo travaso di informazioni fra gli stabilimenti e i magazzini.
È fondamentale superare quell’approccio a “compartimenti stagni” dove la produzione, la pianificazione, il magazzino lavorano ognuno per i propri obiettivi
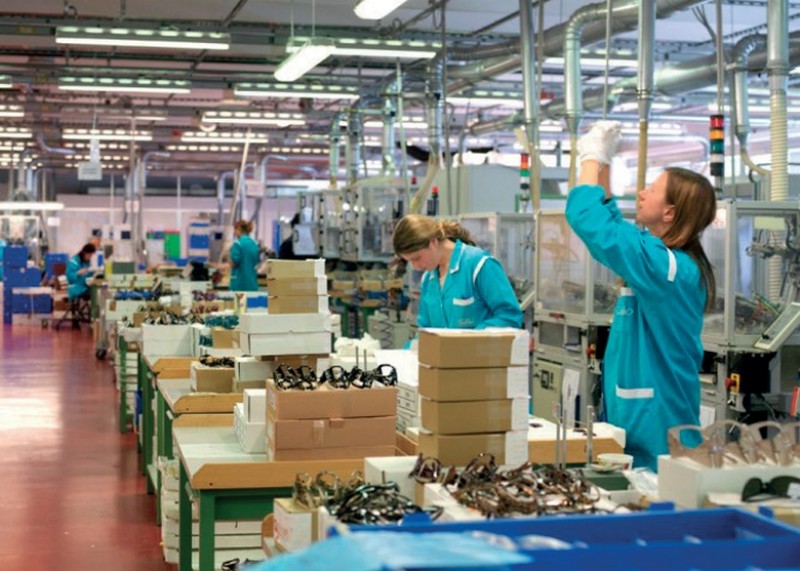
DALLE PREVISIONI ALLA GESTIONE DELLA DOMANDA
Vediamo dunque il processo nel dettaglio. La sede centrale di Padova riceve un forecast da tutte le regioni del mondo. A partire dal forecast si determinano i requirement di produzione globali, affinché si possano effettuare gli acquisti di materia prima. Questo tipo di pianificazione deve essere effettuata globalmente, perché i plant sono strettamente interconnessi fra loro. Vi è poi la pianificazione locale, che consente di gestire correttamente gli eventuali constraint, evitando che interrompano il resto della catena produttiva – l’esempio classico in questo senso è il periodo di Capodanno cinese, che impatta sulla produzione di tutti gli altri plant. La distribuzione, infine, deve essere ottimizzata, avendo come duplice obiettivo la necessità di evitare l’obsolescenza e l’eccesso di prodotto, oltre che lo stock-out: visto che l’obiettivo non può essere produrre esattamente ciò che vorremmo che il cliente comprasse, dobbiamo sapere per quanto possibile in anticipo ciò che il cliente vorrebbe comprare, e produrre, o distribuire, di conseguenza.
L’informazione di partenza proviene dunque dal Sales Planning, che è la prima interfaccia fra mondo commerciale e mondo della pianificazione. Questa informazione viene elaborata dal Global Demand Planning per generare la pianificazione di dettaglio sulle SKU. Distribution Requirement Planning ed Enterprise Supply Planning, con JDA, diventano Central Supply Network Planning, ovvero una pianificazione centrale che gestisce i requirement, integrata con la pianificazione locale e per singolo brand. Siamo già in ottica “control tower” quindi con la possibilità di gestire i dati centralmente.
Il framework di pianificazione integrata parte sostanzialmente dal Forecast, opportunamente interpretato con gli algoritmi previsionali legati alle caratteristiche del prodotto, del canale e così via, tenendo conto anche della complessità dovuta alle SKU di nuova introduzione, per le quali non è disponibile una serie storica. Questi dati sono trasmessi dal Demand Planning al Distribution Requirement Planning, che consiste in sostanza nel classico “netting” fra la giacenza disponibile, i dati previsionali e dunque gli ordini di produzione. Con JDA si parla di Enterprise Supply Planning – ovvero la possibilità di gestire centralmente tutti i requirement, per smistare la produzione sui diversi plant a livello globale – e, infine, si può passare in questa fase dalla pianificazione all’esecuzione: avremo quindi il piano generale di produzione e di acquisto, il Manufacturing & Purchasing Planning Execution. Dopo la fase in cui viene realizzato il prodotto di cui c’è effettiva necessità, ancora una volta il Distribution Requirement Planning avrà il ruolo di ottimizzare le giacenze disponibili e aumentare il livello di servizio al cliente. L’esecuzione di magazzino, infine, si occuperà di realizzare la movimentazione stabilita.
Oggi la piattaforma di Safilo è completamente integrata, ma il progetto con JDA è stato svolto per passi successivi. Si è partiti prima con un orizzonte europeo per poi allargare il progetto al mondo intero. Tutte le forze vendita inviano le proprie previsioni ad un solo punto centrale; ma, visto che queste proiezioni riguardano gli stessi prodotti, che devono insistere sugli stessi fornitori e sugli stessi stabilimenti, come step successivo si è passati ad un collaborative forecasting, per combinare insieme tutti gli ordini al fine di ottimizzare la domanda, evitandone gli eccessi. Di certo, il progetto svolto con JDA ha consentito a Safilo di ottenere un livello di visibilità finora non possibile: oggi l’azienda conosce ogni singolo pezzo presente in ogni singolo magazzino nel mondo. Cosa che consente anche di movimentare (in gergo “deployment”) parti di stock in base al bisogno che si può avvertire in altre aree geografiche.
Dobbiamo sapere per quanto possibile in anticipo ciò che il cliente vorrebbe comprare, e produrre, o distribuire, di conseguenza.
DALLA PIANIFICAZIONE GLOBALE ALLA PIANIFICAZIONE LOCALE
Lo step finale del progetto, tuttora in corso, riguarda in particolare gli ordini di produzione, che sono diretti a sette stabilimenti fra Italia ed estero. La pianificazione centrale decide le assegnazioni e le tempistiche, e suddivide il carico di produzione nei singoli stabilimenti. Ricordiamo il fatto che gli stabilimenti possono produrre semilavorati diretti ad altri stabilimenti, oppure prodotti finiti che a loro volta ricevono semilavorati da altri stabilimenti. Chiaramente, un qualsiasi ritardo di un qualsiasi stabilimento impatta pesantemente sull’attività finale; oppure, sapendo in anticipo che una qualsiasi fornitura sarà in ritardo, il plant ricevente potrebbe anticipare risorse per avanzare altre produzioni. Qui nasce il concetto di collaborazione tra plant; la pianificazione centrale comunica le assegnazioni ai singoli plant, su un orizzonte temporale diciamo di quattro mesi; ma le pianificazioni locali, il cui orizzonte temporale è più limitato, diciamo quattro settimane, possono comunicare con esattezza se riescono a rispettare quelle assegnazioni oppure no.
I vincoli di ciascuno, infatti, si ripercuotono sulle performance di tutti gli altri plant. Si porta quindi a livello di pianificazione, di Enterprise Supply Planning, la “distinta base” di tutti i prodotti dei singoli stabilimenti, lavorando soprattutto sui materiali critici, quelli che hanno maggiormente impatto sul resto della produzione o comunque sul lavoro degli altri plant. In questo modo, anche se si verifica un ritardo, questo impatta in misura limitata sull’esito finale della produzione, in quanto, potendo comunicare tempestivamente la pianificazione di ogni singolo stabilimento, gli stabilimenti successivi possono organizzarsi in anticipo in modo da assorbire tale ritardo, reagendo in tempo e cambiando i propri piani in modo da sfruttare al meglio le proprie risorse.
LA COMPLESSITÀ DEL PROGETTO: NON SOLO TECNOLOGIA
Abbiamo visto dunque lungo la catena diverse tipologie di soggetti e relative funzionalità – Sales Planning, Demand Planning, Central Supply Planning… - che oggi sono in grado di scambiarsi informazioni reciprocamente, grazie ad un layer ulteriore di raccolta dati con cui ogni punto della catena entra in una relazione costruttiva con il passo successivo. Chiaramente, l’apporto tecnologico è stato determinante, ma va anche detto che l’ostacolo più impegnativo da superare è sicuramente quello organizzativo. Secondo il relatore, infatti, è fondamentale superare quell’approccio a “compartimenti stagni” dove la produzione, la pianificazione, il magazzino lavorano ognuno per i propri obiettivi. Pertanto, in parallelo all’introduzione del nuovo sistema che aveva come obiettivo l’integrazione di tutta la filiera, anche l’organizzazione è stata via via portata a strutturarsi in modo più coordinato e coeso.
Per mettere in comune le informazioni di pianificazione, con quelle del magazzino, della produzione e della distribuzione, è necessario sì trovare lo strumento tecnologico in grado di farlo - con la potenza di calcolo adeguata per gestire grandi volumi di dati sostanzialmente in tempo reale e un database unico in grado di supportare un simile modello - ma anche aprire l’organizzazione a questo cambiamento. Alla base quindi vi è la volontà di costruire un processo, un approccio integrato, nel quale ogni funzione sia messa in condizione di dialogare pienamente con quelle adiacenti, anche per poter sfruttare al meglio le possibilità tecnologiche offerte dal sistema.
In tal senso il workshop organizzato dal Club Produzione e Tecnologia della SDA Bocconi ad inizio marzo, dedicato proprio al concetto di Supply Chain Control Tower, puntava appunto ad esplorare non solo le opzioni tecnologiche necessarie per realizzare tale concetto nella pratica, ma anche e soprattutto la necessità di coinvolgere tutta l’organizzazione in un progetto che di fatto coinvolge profondamente tutte le sue parti principali. Il caso proposto da Safilo è certamente esemplificativo della necessità di utilizzare questi sistemi per reagire al meglio alle sfide del comparto fashion, ma anche contesti come l’e-commerce, la multicanalità, l’evoluzione in atto nei diversi settori della distribuzione, impongono alle aziende di diventare sempre più reattive e flessibili, e per questo risulta cruciale uno strumento in grado di fornire piena visibilità su tutta la supply chain. Una control tower, insomma, in grado di legare stabilmente e reciprocamente pianificazione ed esecuzione, produzione e distribuzione.